When ice cream melts in your hands on a hot day, it can be a bit frustrating; but if a load of vaccines can’t be used because it went bad due to improper storage or transportation conditions, the results are a lot more serious, if not fatal.
There are a number of food products, medications, and other goods that have to be maintained at a certain temperature. So, it’s important that all supply chain parties (3PLs, carriers, storage facilities, etc.) dealing with such goods understand how to handle them correctly. In this post, we’ll talk about what cold chain logistics is, how to manage it at different stages, and which technologies support these activities.
What is cold chain logistics?
A cold chain is a supply chain that deals with perishable, temperature-sensitive goods (also called cool cargo) such as fresh produce, meat, dairy, seafood, chemicals, pharmaceuticals, flowers, wine, etc.
Usually, a specific low-temperature range has to be maintained to ensure the quality and integrity of perishable goods, i.e., some groups of products have to be refrigerated, some must be frozen, while yet others require extreme conditions (a so-called ultralow chain or deep freeze). Failure to maintain the right temperature leads to product spoilage and, ultimately, financial losses.
Cold chain logistics is a set of activities aimed at handling and transporting such items securely from the manufacturer or supplier to consumer.
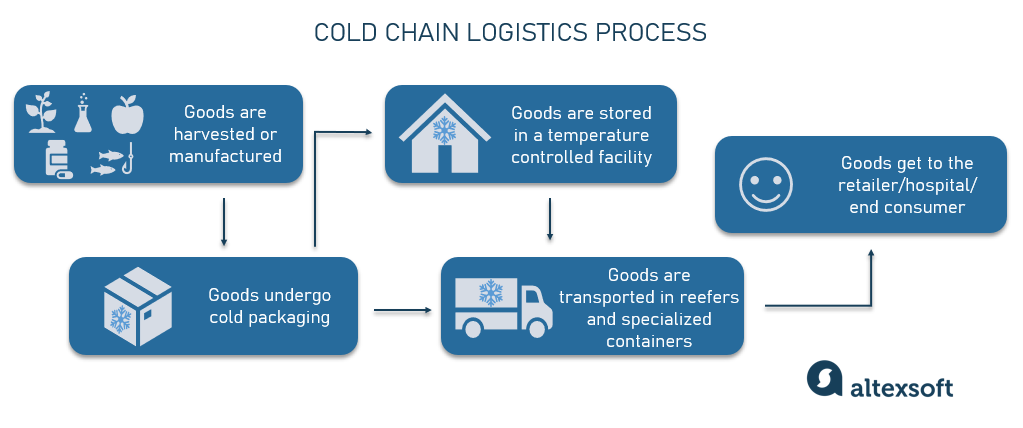
A common cold chain scenario
Obviously, the longer the journey between the original supplier and end consumer and the more legs (and/or transportation modes) involved, the more difficult it is to maintain the necessary temperature. For example, in the case of international shipping, freight sometimes goes through multiple storage facilities or distribution centers and has to be reloaded several times. Unless items are permanently kept in a sealed refrigerated container, all these activities increase the risks of temperature fluctuations.
Within the cold chain logistics process, the packaging, storage, and shipping stages cause the greatest complications.
Cold chain packaging
Ensuring optimal temperature starts with selecting the proper type of packaging, container, and refrigerating method. All that, in turn, depends on multiple factors, such as
- type of cargo,
- required temperature and humidity levels,
- size of shipment,
- duration of transit,
- outside temperature (it’s especially important in case of climate changes for long-distance shipments), and so on.
For every type of temperature-sensitive shipment, different packaging is used. For example, vaccines are transported in small insulated boxes, while 53 foot reefers with inbuilt refrigerating units are used to haul foodstuff. We’ll talk more about packaging technologies in one of the next sections.
Cold chain storage
Warehousing is a complex system that involves numerous processes from storage itself to consolidation/deconsolidation to loading/unloading. Within cold chains, specialized warehouse facilities also often offer such focused services as blast freezing, precooling, frozen receiving, ripening, inspection checks, and so on.
At this stage, it’s important to design appropriate facilities with optimal climate control (both for storage and loading areas) as well as implement certain practices when handling perishable goods.
Cold chain shipping and tracking
As we mentioned above, transporting cool cargo requires specialized equipment known as reefers or freezers. Those are special refrigerated trucks, railcars, cargo ships, and aircraft. Often, not only temperature but also humidity must be controlled, so such equipment has to be capable of that as well.
There’s one more process that’s hard to put in a stage sequence but that’s still crucial in any supply chain. Tracking shipments while en route is always important, but in the case of cold chain, monitoring cargo environmental conditions is essential to ensure efficiency. Shippers, carriers, and consignees alike want to have access to monitoring data for quality assurance and performance assessment.
Cold chain logistics use cases
Multiple industries, including agriculture, manufacturing, and healthcare, strongly rely on cold chain logistics to safely store and transport perishables. Today, the need for such services keeps increasing due to changing consumer demand, trends like “from farm to fork,” and the necessity for new drugs and vaccines. Let’s look closer at industry sectors that need cold chains the most.
Cold chain in food industry
Storing and transporting perishable food products is the oldest and most obvious cold chain use case, originating centuries ago to avoid rot or mold. We all know from our middle school (and our own experience) that the quality of certain food categories degrades with time because of natural chemical reactions – reactions that can be slowed down with lower temperatures.
There are several categories of food that require different thermal conditions.
Banana. Tropical fruits like bananas or pineapples undergo controlled ripening as they are transported, so they need a stable range of 12° to 14°C (53° to 57°F).
Chill. Most vegetables, fruits, dairy products, and meat must be refrigerated around 2° to 4°C (35° to 39°F).
Frozen. Meats, bread, cakes, and most other products that need freezing require temperatures between -10° and -20°C (14° to -4°F).
Deep-frozen. Seafood, ice cream, and some other items have to be deep-frozen or stay between -25° to -30°C (-13° to -22°F).
Cold chain in pharmaceutics
The demand for cold chain logistics services in pharma has grown steadily over the last few years. The 2020 Biopharma Cold Chain Sourcebook predicts that this market will be worth $21.3 billion by 2024 (up from 2019’s $15.7 billion). Blood, stem cells, tissues, transplant organs, as well as diverse drugs and vaccines – all these items need a range of 2° to 8°C and sometimes down to -80°C. If the required temperature level is not maintained, such products can become useless or even harmful for patients.
Recently, billions of COVID-19 vaccines had to be spread out on a global scale – and they require a stable, ultra-low temperature of below -70°C (so do some others, including the Ebola vaccine). Besides, a large number of new drugs being approved by the US Food and Drug Administration is temperature-sensitive as well. So, the need to develop proper cold chain infrastructure to maintain required conditions at all stages is higher than ever.
Typically, if pharma goods have to be shipped urgently, they are transported by air. However, if time is not critical, ocean transportation is preferred because it’s cheaper and safer (i.e., less subject to temperature breaches).
Also, in contrast with the food industry, there is a higher demand for packaging options and containers that can maintain ultra-low temperatures. So, let’s finally discuss which special materials and equipment are commonly used in cold chains to protect the integrity of shipments.
Cold chain equipment and packaging options
We’ve already indicated that usually reefer trailers, diverse containers, and even specialized vessels are used to transport temperature-sensitive products. Liquefied gasses (such as oxygen, nitrogen, argon, CO2, etc.) are stored and transported in special cryogenic tanks, trailers, and railcars.
Meanwhile, for storage purposes, warehouse/terminal facilities and distribution centers are equipped with capacious walk-in coolers and refrigerators that maintain a stable temperature. To store pharmaceuticals, drugs, tissue samples, and other medical items, there’s a wide variety of laboratory refrigerators and freezers capable of supporting the required temperature.
As for packaging, there’s a huge range of cooling products to keep perishables cold. There are two main categories of such technologies.
- Passive cold containers rely on dry ice, gel packs, gel bottles, liquid nitrogen, eutectic plates, quilts, and other cooling/auxiliary stuff to keep the internal temperature low. Pharma products can be more demanding and require ultra-low freezing, so specialized containers are being developed to satisfy industry needs.
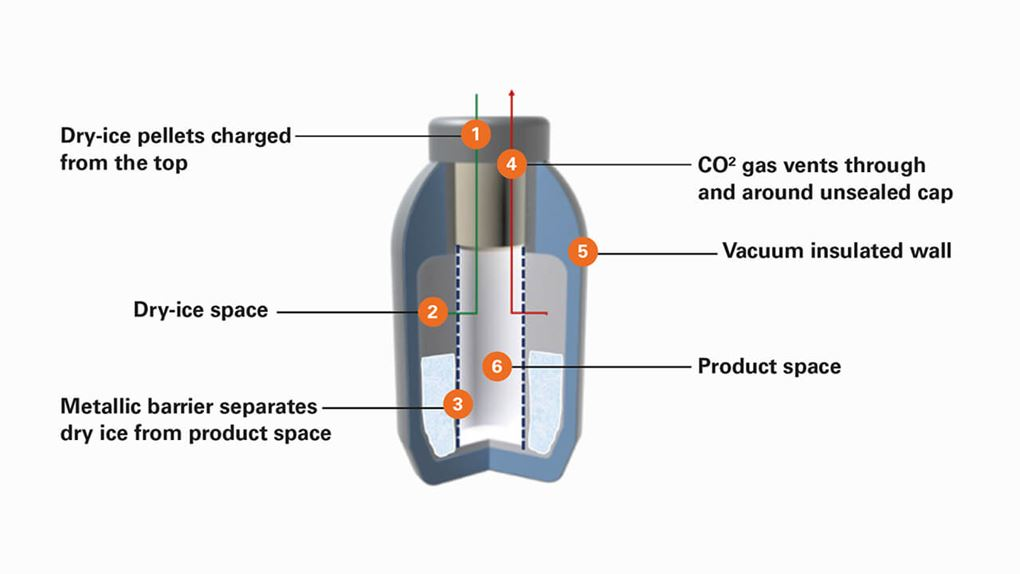
Innovative CryoSure containers can keep vaccines safe at -70°C for up to 3 weeks
2. Active cool containers can monitor and control the internal temperature level. Such powered refrigeration units include sensors, a control unit, and ventilators that adjust the temperature automatically to keep it stable.
Comparing the two, active containers seem pricey at first, but they often turn out to offer more cost savings than traditional passive ones. They are reusable, take less space, require less handling, don’t need cooling material replacing, provide better guaranteed temperature control, and can be shipped with other cargo or as LTL freight (which is cheaper than hiring dedicated reefers).
In addition, active containers include a monitoring device that provides an opportunity to track shipments and related activities. Let’s look deeper into which technologies make it possible.
Cold chain digital technology
We’ve already mentioned the importance of complete visibility in cold chain logistics. Most temperature-sensitive products are also time-sensitive, and despite proper storage conditions, they have to be transported without delays.
So, all stakeholders want to track such vulnerable cargo and constantly monitor its condition not only to be aware of what’s going on but also to be able to react quickly in case of any deviations. And that’s what modern digital technology can help with.
Tracking
For tracking purposes, you can take advantage of such technologies as
- global positioning system (GPS),
- global system for mobile communication (GSM),
- radio-frequency identification (RFID), and
- Bluetooth low energy (BLE).
If cold cargo is hauled by truck, telematics solutions powered by GSM/GPS allow for tracking the vehicle’s position in real time while en route. Typically, location data is sent to the carrier’s transportation management system (TMS) or other business solution in use. Many carriers, in turn, provide their customers with access to tracking information via customer portals, or, at least, a link to the third-party tracking service provider.
Attaching battery-powered GPS devices to the shipping containers makes it possible to track their location whether they are transported by trucks, rail, or ships. Typically, cold chains prefer the ones that also have a monitoring functionality – we’ll talk about it in the next section. Data from such trackers gets to the carrier’s or shipper’s business management solution.
As for maritime shipping, major ocean carriers provide their vessels' satellite location data through their websites/apps/customer portals, as do 3PLs and freight forwarders that deal with international shipping.
There’s also a number of independent global sea data providers such as MarineTraffic that show real-time vessel position. Whichever way you choose, nowadays it’s fairly easy to sit back and watch how your cargo is being moved around the globe.
RFID and BLE work in a different way. Tags or beacons have to be attached to containers or individual packages and scanned to fetch data. We’ve all seen anti-theft alarm systems in stores – that’s how RFID works.
RFID tags can be passive or active. Passive tags don’t have a power source and are activated by the reader. Active ones have an inbuilt battery, so they broadcast their own signal, can be scanned from a greater distance, but not surprisingly they are much more expensive and bigger in size.
RFID and BLE readers are usually installed at checkpoints (e.g., at terminals or distribution centers) so that they automatically scan all the tags/beacons within their working range. There are also handheld RFID readers, while BLE beacons can be scanned with a smartphone (which is their big advantage as it’s really cheaper). The data is then sent to the ERP, terminal operating system, warehouse management system (WMS), or other integrated business solution.
Please see the brief comparison of main tracking technologies in the table below. To sum it all up, GPS devices are perfect for real-time global/outdoor container or equipment tracking (but they are very costly and have shorter battery life), while RFID/BLE technologies work best for indoor use and receiving periodic information on individual packages.
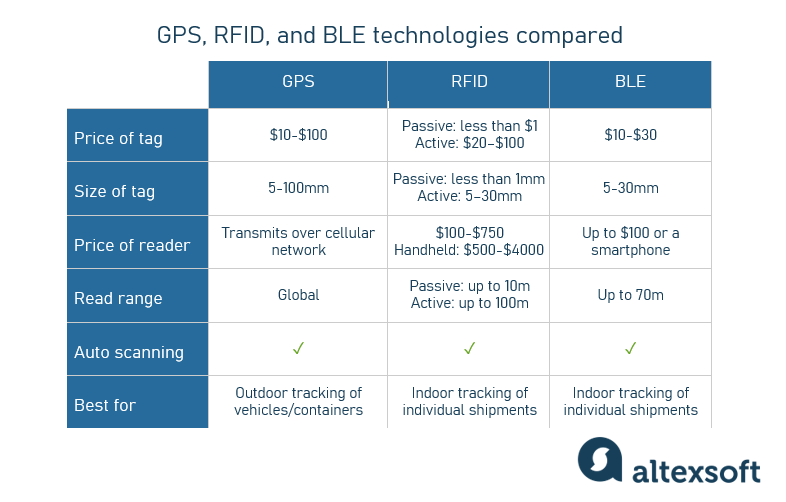
GPS vs RFID vs BLE for supply chains
Monitoring
The GPS and RFID technologies we described above work great for tracking purposes, but they can’t do measurements, store records, and transmit them. To monitor temperature, humidity, and sometimes even vibration, other types of devices are used in cold chain logistics, helping stakeholders ensure a safe and stable environment. Here are some of them.
Data loggers are the most typical monitoring solution. These devices are placed inside the container (or storage area) to measure temperature (and sometimes humidity as well) at regular intervals. They keep records of shipping/storage conditions that can be extracted by physically connecting to a data logger.
It’s a cost-effective solution, but its drawbacks are obvious: no real-time monitoring and the need to be in close proximity to retrieve data.
Bluetooth temperature sensors (that’s the same BLE technology we mentioned above) are more advanced as they can also add location data to temperature measurements and transmit records wirelessly when scanned with a reader or a smartphone.
However, they still don’t provide real-time monitoring by themselves. To receive live updates, they have to be connected to an IoT infrastructure.
IoT is all about connectivity and real-time data (well, in our case it’s almost real-time; usually, measurements are made every few minutes). A typical IoT infrastructure for cold chains includes
- BLE sensors that are attached to containers, packages, or pallets and that measure temperature and sometimes humidity, CO2 level, and so on;
- a portable gateway hotspot that collects measurements from the sensors and transmits records to the virtual storage;
- a cloud storage that receives records, stores them, processes, and allows for retrieving data when needed; and
- a user-facing app or platform (e.g., ERP, TMS, WMS, other business solution or specialized software) that visualizes information for users via dashboards and reports.
You can read more about how IoT works in our dedicated article.
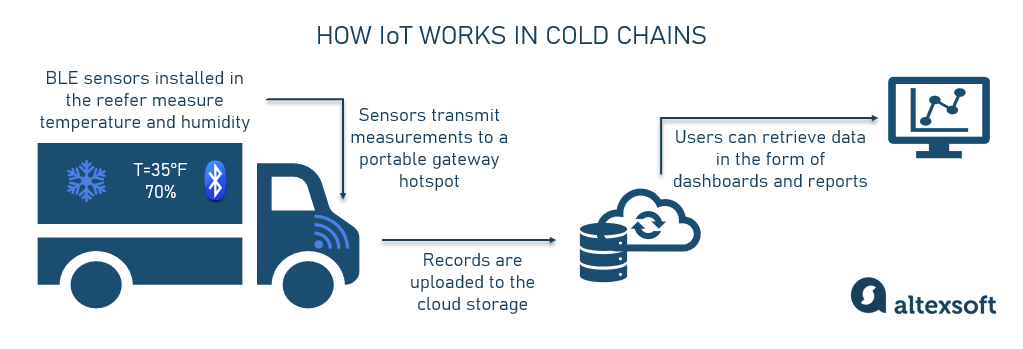
Typical IoT architecture in cold chains
Such smart systems not only enable real-time monitoring, but can also be configured to send alerts in case of temperature breaches or other abnormal events.
Integrating tracking and monitoring solutions
If you have just a few shipments in your cold chain, you can track them through a customer portal provided by a carrier. However, if you operate multiple shipments regularly, you need a more convenient way to track your cold cargo and ensure it’s safe.
As we said, you can install your own GPS tracking devices or design an entire IoT infrastructure to monitor all important indicators. But if you rely on the carrier to handle these activities, consider building an integration between your systems. It takes development effort, time, and investment, but the rewards are convenience and saved time.
As you establish such an API connection, you’ll be able to receive location, temperature, and other important information from the carrier/3PL right to your internal system. That will allow you to monitor the status of your shipments and timely react in case of disruptions.
Cold chain standards and regulations
Since cold chains deal with very delicate and sometimes vitally important goods, there are multiple regulations and requirements set by various government institutions to ensure safe storage and shipping. Standards are established in relation to temperatures, timing, packaging, supporting documentation, and much more. We’ll only list the main regulators.
- The US Food and Drug Administration (FDA) develops standards that cover the entire supply chain from production to packaging to storage to last-mile delivery to documentation.
- In Europe, the Good Distribution Practice (GDP) is a main set of standards that all distributors of medicinal products must comply with.
- The World Health Organization (WHO) created Guidelines on the international packaging and shipping of vaccines to regulate pharma cold chains.
- The International Air Transport Organization (IATA) issued Perishable Cargo Regulations that contain guidelines on shipping sensitive products.
Additionally, IATA's Temperature Control Regulations (TCR) were set apart as a standalone publication to ensure safe air shipping of pharmaceuticals. TCR requires special Time and Temperature Sensitive Labels to be used. Also, since 2013, aircraft operators and ground-handling agents must verify their compliance according to IATA’s Standard Acceptance Checklist.
Other regulating bodies like the European Parliament, US Customs, the Transportation Security Administration (TSA), or the Department of Transportation (DOT) also have their requirements, but they concern usual supply chains as well. Besides that, each country has its own regulations.
Worth mentioning separately is the Global Cold Chain Alliance (GCCA). GCCA unites 1,100 cold chain logistics service providers in 85 countries and its mission is to build a universally strong and safe cold chain. Together with its core partners, GCCA develops best practices and guidelines, provides advisory services to governments and organizations, conducts assessments and research, and serves as a universal voice of the cold chain industry.
Cold chain logistics companies
Both shippers and 3PLs/carriers encounter lots of complexities at each stage of the cold chain process. So, it’s not uncommon to outsource at least part of the job to third-party cold service providers.
Shippers can definitely use the services of such major carriers as FedEx or UPS to transport their perishables, but specialized companies have developed a niche logistical expertise that allows them to professionally handle temperature-sensitive products for their clients. But where to find a reliable partner?
For that, we can turn to the global top-25 list, published annually by the International Association of Refrigerated Warehouses (IARW). These are the top three refrigerated warehousing and logistics providers as of March 2022.
- Lineage Logistics is an undisputed, permanent global leader of the food cold chain providers with its capacity of 2.6 billion sq. ft. (73.5 million sq. m.). It operates a network of over 400 facilities in 19 countries and is known for its tech innovations (see its Lineage Link supply chain management platform) and sustainable approach.
- Americold Logistics, founded in 1903, has a capacity of 1.4 billion sq. ft. (40 million sq. m.) and 250 facilities. It also provides transportation and warehousing services as well as technology solutions (check its i-3PL supply chain control system).
- United States Cold Storage, whose capacity is 423 million sq. ft. (12 million sq. m.) in over 40 facilities, is the third-largest provider of warehousing, transportation, and other logistics services.
As you may have noticed, these companies specialize in food cold chain logistics. To ship pharmaceuticals, it might be worth cooperating with such niche specialists as Envirotainer, PCI Pharma Services, or BL Turkey.
Cold chain logistics challenges
Shippers are ready to pay for secure cold storage and transportation to prolong the product shelf life and satisfy customer demand. However, carriers and 3PL companies face multiple challenges that make cold chains a tough business.
Creating and maintaining infrastructure. The 26th Annual Third-Party Logistics Study released in September 2021 revealed that the majority of 3PLs reported investing in a cold chain infrastructure and maintaining it, and temperature monitoring as their main issues. To meet shippers’ requirements, 3PLs are forced to have a range of different equipment from coolers to deep-freezers, and invest in new technologies.
Proper handling. According to the same study, proper handling was the biggest challenge for shippers. To ensure product quality, certain sanitation, packaging, cleaning, sorting, and other practices have to be implemented.
Regulatory compliance. Multiple regulations keep all supply chain participants on their toes and make them invest in modernization to comply, especially in the aspects of goods traceability and visibility. Plus, temperature records have to be documented and stored correctly.
Other industry problems range from insufficient specialists to high spend on electricity. But despite all the issues, 91 percent of shippers and all 3PLs who took part in the research expect an increase in demand for cold chain capacity over the next three years. Intelligent businesses realize the importance of modernization and investment since it’s already clear that the future of cold chains is behind innovative technologies.
Read how supply chains can benefit from using AI, ML, and other modern technologies in our dedicated articles:
How to Solve Vehicle Routing Problems: Route Optimization Software and Their APIs
RTLS in Warehouses: Boosting Efficiency with IoT-Based Systems
Load Planning Software for LCL, Consolidated, and FCL Shipments
Supply Chain Analytics: Opportunities in Data Analysis and Business Intelligence
Demand Forecasting Methods: Using Machine Learning to See the Future of Sales
Inventory Management Software: How Technology Addresses Inventory-Related Issues
Robotic Process Automation (RPA) in Supply Chain Management: Use Cases and Implementation Tips
Integrating Shipment Tracking: Shipping APIs and EDIs from Major Carriers and Aggregators
5 Ways AI Will Transform the Logistics Industry
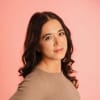
Maria is a curious researcher, passionate about discovering how technologies change the world. She started her career in logistics but has dedicated the last five years to exploring travel tech, large travel businesses, and product management best practices.
Want to write an article for our blog? Read our requirements and guidelines to become a contributor.