A warehouse (fulfillment/distribution center) is a complex system with multiple components that have to work together like a well-oiled machine. And, just like with any sophisticated structure, there’s a number of challenges that warehouse managers have to overcome to ensure effective, continuous operation.
In addition to age-old problems of asset misplacement, theft, and employee injuries, today’s competitive landscape poses huge challenges related to increasing efficiency and speed of operations. To succeed, digitization is a must, and it’s not only about replacing personnel with robots and autonomous vehicles.
Real-time tracking systems and advanced analytics software can optimize warehouse workflows. In this article, we’ll talk about the nuances of RTLS choices, implementation, and integration in warehousing environments.
What is RTLS and which warehouse challenges does it address?
An RTLS or real-time location system is an autonomous, IoT-based network of connected devices that enables tracking and identification of objects. Simply speaking, a multitude of little tags are attached to equipment/vehicles/pallets/other items – or carried by employees (for example, embedded in staff access cards). These tags transmit information in real time (or near real time) to so-called anchors (readers/antennas/receivers) installed all over the place (ceilings, walls, shelves, etc.). Then all this data is transferred to the cloud for storage and processing.
Depending on whether tags are sensor-enhanced or not, transmitted data can include
- identification information,
- location,
- time,
- asset condition and/or maintenance status,
- environmental information (temperature, humidity, etc.), and so on.
Because of its cost, real-time tracking can’t completely replace traditional inventory management approaches based on barcodes and other simple scanning systems. So, RTLSs are implemented to track high-value assets/inventory or big shipments, in addition to monitoring equipment/personnel performance in industrial environments, warehouses, yards, ports/terminals, etc. Such systems are also used for tracking people within the facility for security, navigation, or analytics purposes.
So how can real-time tracking help address warehouse challenges? Let’s talk about your probable pain points as a warehouse manager.
Misplaced inventory and equipment. How often do you have your workers go pick stuff and come back with nothing because the needed items just weren’t there? It’s a very common problem: Goods are often put in wrong locations, while forklifts get “lost” somewhere in pathways, making workers waste lots of time just looking for things. Delivery speed suffers a lot, leading to transportation delays and customer dissatisfaction. Tagging pallets and handling equipment with smart devices will allow you to always know where your inventory and assets are.
For example, an RTLS installation helped HANGCHA (one of the leading handling equipment manufacturers in China) to reduce search time from 10-15 minutes to just 1 minute – a dramatic increase in productivity.
Inefficient picking process. Manual, paper-based picking processes are time-consuming and error-prone. It takes forever to find the right location and then make sure that’s the right box – all that with hands limited by paper picking lists. Having an intelligent RTLS in place, staff gets clear instructions from wrist computers, AR-glasses, or machine-mounted tablets (sometimes audio devices are also used).
AR glasses. Source: Pozyx
This way, personnel have their hands free and always know the best way to get where they need to go. Speaking of which…
Nonoptimal routes. No one wants warehouse employees to wander around in circles trying to locate the needed goods, but that’s what often happens, especially in large facilities. RTLSs can build optimal routes for different processes to speed up operations. Besides, optimal routes usually mean shorter distance traveled, resulting in less fuel used and more costs saved.
Congested pathways. That’s another problem related to inefficient planning. Sending several forklifts to the same aisle poses security risks and can cause delays. An RTLS dynamically reroutes workers or reorganizes tasks to avoid congestion.
Underutilized equipment. All business owners strive for efficient use of resources and don’t want their staff idle or their equipment underutilized. RTLSs give a per-unit visibility into historic asset performance making it easier to detect inefficiencies and areas for improvement. For example, you’ll be able to monitor such important handling equipment metrics as distance traveled, time needed for task completion, number of loaded/unloaded trips, idle time, etc. to see optimization opportunities.
Underutilized storage space. Knowing driving patterns will help you find ways to optimize storage space usage, e.g., put items with the highest turnover into the most accessible locations. After implementing an RTLS, Volkswagen’s warehouse area “has been expanded” by 20 percent just by improving utilization.
Asset downtime. Sudden equipment breakages or malfunctions can be the reason for significant operational disruptions, and preventative maintenance doesn’t always help. Unplanned downtime is estimated to cost industrial manufacturers $50 billion annually. Advanced asset tracking systems enable predictive maintenance by providing regular automatic reports on asset health and sending alerts in case of any abnormal functioning. As a result, timely repairs minimize downtime, increase overall operational efficiency, and help cut expenses on fixing potentially serious issues.
Asset theft. Nowadays, even forklifts get stolen. Not to mention retail inventory shrinkage which, by the way, is an almost $100 billion problem, according to the 2022 National Retail Federation’s Security Survey. Using real-time asset tracking devices helps reduce the number of missing items. Geofencing or setting up automatic alerts in case tagged assets leave the designated zone is an efficient solution to this problem.
Security issues. Moving machinery, falling objects, hazardous goods, floods, fires, and other risks make warehouses a dangerous environment to work in. But if your employees wear trackable tags, you can always make sure everyone left the unsafe zone in case of emergency. Such virtual geofencing will allow you to set up alerts when someone enters a restricted/dangerous zone or exceeds dwell time. Also, alerts can be sent to equipment drivers if other people or machines get in close proximity.
Lack of visibility into operational processes. Having all tracking data in a single system provides a holistic view of your assets’ location, usage, condition, and lifespan as well as of operational workflows. Centralized access to data enables business intelligence and streamlines reporting, planning, and decision-making processes.
Motion history by WISER RTLS
As you can see, an RTLS elevates traditional asset/inventory tracking (which only provides intermittent information relying on barcodes or passive RFID tags) to a new level – continuous monitoring. So let’s see which technologies make it possible.
Main networking technologies used in RTLSs and how to choose one
There’s a huge variety of tracking technologies, but only four of them serve as an effective basis for indoor RTLSs: active RFID, BLE, Wi-Fi, and UWB.
All of them operate on the RF basis, have inbuilt batteries to power continuous data transmission (though their duration of operation can differ), and can be sensor-equipped to enable the transmission of additional information (besides solely ID and location). But before we discuss them in more detail, here are the key parameters that we’ll compare them by.
Read range. The bigger the read range of the anchors, the fewer of them you’ll have to install.
Accuracy. Different technologies allow for different positioning accuracy, from sub meter precision (UWB) to 15 meters (Wi-Fi). If you need to track a few vehicles in an open area, you might not need super-accurate tracking but if you want to locate a specific box or pallet in a densely packed room, consider technologies with higher precision.
Pricing. The price range of tags and anchors is wide, and if you have a big facility, you’ll need a lot of them, so this factor is sometimes decisive.
Battery life. Besides purchasing tracking devices themselves, you’ll have to replace batteries that power your tags. If you install hundreds or thousands of them, the bucks pile up. Low-energy tags have long-lasting batteries (and consume less energy which also leads to cutting costs) so that’s a way for you to save money and effort.
So here’s a brief description of the most widespread wireless networking technologies used in indoor RTLSs.
Main real-time tracking technologies compared
RFID: a classic approach
Passive RFID tags that are activated with a radio frequency signal from a scanning device can’t be used with an RTLS because they don’t have real-time tracking capabilities. So, we’ll only discuss active RFID tags. With a read range of up to 100 meters (300 feet) and location accuracy of 2-3 meters (7-10 feet), active RFID labeling is a popular approach to indoor asset tracking as well as container/pallet-level tracking of shipments in warehouses.
The weakness of RFID technology is interference caused by RF transmitters in the area of reach (such as Wi-Fi access points). Also, even though the tags are relatively inexpensive (around $20-30), the readers are quite costly ($1-5k), which accounts for high initial implementation costs.
Bluetooth: an energy-efficient, highly compatible solution
Bluetooth Low Energy (BLE) gained wide application in IoT tracking systems becoming an industry standard for indoor RTLSs. BLE tags or beacons are designed to be very energy-efficient. Another big advantage is that they are easily compatible with multiple types of devices that support Bluetooth including smartphones, computers, and so on. Various Bluetooth-enabled devices are used for reading beacon signals, and even specialized readers are much cheaper compared to RFID ones.
BLE beacons transmit data for a range of up to 100 meters (300 feet) and allow for positioning accuracy of 1-2 meters (3-7 feet).
Among BLE technology’s drawbacks are latency (BLE tags “sleep” until they sense the reader signal – which is why they use less power), signal interference, and security vulnerabilities.
Wi-Fi: makes use of existing infrastructure but lacks accuracy
Wi-Fi-based asset tracking systems connect to existing networks to transmit real-time location. Since no additional network infrastructure is required, their implementation is usually inexpensive (though Wi-Fi tags are quite costly). Also, large amounts of data can be quickly transferred over Wi-Fi networks. Yet Wi-Fi devices alone can only provide basic location information. To transmit more details, BLE or UWB solutions have to be implemented.
Another downside is that Wi-Fi tags are less power-efficient than, say, BLE beacons, so the batteries have to be replaced more often. In addition, this tracking method doesn’t give high precision, offering an accuracy of around 15 meters (50 feet) – unless you install a really dense network of readers – and is prone to signal interference and security issues.
So warehouse RTLSs are seldom based solely on Wi-Fi-enabled tags, but many IoT systems make use of Wi-Fi networks to pass signals from receivers or readers to the storage/processing platform. In fact, today, enterprise-grade Wi-Fi points of access are often made with BLE technology already built-in.
UWB: high-precision solution that’s least sensitive to RF interference
UWB or ultra-wideband is another radio technology for indoor tracking that’s gaining traction. UWB tags are power-efficient, have a range of up to 100 meters (300 feet), and have a high rate of data transmission (up to 110 Mbit/sec). They also don’t interfere with other RF transmissions which is important in industrial and logistics environments.
UWB’s main advantage is precision – it provides location accuracy of up to 10-30 cm. However, such precision is achieved only when tracked assets are in a clear line of sight of scanning devices – and within the reading range. That makes their implementation more complicated than that of BLE or RFID. Also, UWB tags are more expensive than other types.
So which RTLS technology do you need?
Well, the short answer is “It depends.” You have to analyze your existing IT infrastructure (e.g., is it possible to make use of Wi-Fi networks), your specific needs (e.g., how accurate should positioning results be?), and the physical environment (e.g., are there any RF transmissions that can interfere with RTLS readings?).
Most RTLSs today make use of a blend of diverse technologies to achieve optimal results. A common scenario, for example, is a combination of BLE/UWB tags and Wi-Fi transmission capabilities. So let’s discuss the RTLS infrastructure in more detail.
How does RTLS work: IoT infrastructure
The typical warehouse RTLS consists of four main components: tags, receivers or anchors, storage and processing middleware, and a business application. You can get a ready-made solution from one provider that will configure and customize the system for your specific requirements – or purchase each element separately and then connect them into one system. Let’s talk about each of the components.
RTLS infrastructure
RTLS tags
Tags are attached to assets or people and transmit ID/location/time data with a certain regularity (every second, once every several seconds, every minute, etc., depending on the settings). They can be equipped with sensors to track additional readings, LEDs to send visual signals that enable immediate identification, and an alert button to send emergency notifications.
Sewio UWB tags with inbuilt sensors
As we said, active tags have batteries, either built-in or replaceable. The former type is cheaper, but when the battery life is over, you’ll have to buy a new device, while the latter is more expensive but you won’t have to replace the whole thing later on. Most systems today send alerts when the battery is about to deplete.
RTLS receivers/anchors
Receivers are readers installed in the warehouse that form a connected mesh network that picks up signals from tags. Their function is similar to that of satellites in the GPS system if that makes things any easier understand. They are either wired or battery-powered, depending on the vendor and also the location of installation.
The number of anchors you’ll have to install depends on your warehousing environment and your needs, i.e., how big the area is, whether a line of sight can be easily maintained, whether you want 2D or 3D tracking, and so on. For example, 4 UWB anchors can cover an area up to 50x50 meters (164x164 feet) with clear line of sight for accurate tracking.
If you have a challenging environment, talk to an RTLS expert to best plan on the optimal anchor positions. Another option is to devise the RTLS infrastructure yourself with the help of a specialized tool such as Pozyx RTLS Planning Suite.
Planning anchor locations on the warehouse floor map
Typically, receivers also serve as gateways that pass the collected raw data to the cloud or local server via Wi-Fi/Ethernet. In most cases, the more readers you install, the more accurate your tracking will be as they sync data with each other complementing the readings from different devices.
Storage and processing middleware
Storage/processing middleware is basically the server where all the data is stored, plus a location engine which calculates the exact position of tracked objects. It resides either in the cloud or on-premises. Generally speaking, cloud platforms are more scalable and often more powerful, but many companies prefer to keep information on their own local servers for security reasons. Some systems process information on edge (that’s when reading devices have computing capabilities) but it’s rare.
Servers are where raw data is turned into information that’s sent to your business management system for users to work with. The processing solution is connected to business applications via application programming interfaces or APIs.
Some of the popular IoT platforms are IBM Watson, Microsoft Azure, and AWS IoT.
Business application
A business application (either cloud-based or on-premises) is a portal where you’ll be able to actually see all the location data in a readable, interactive form. That’s basically the interface where you can access real-time tracking on 2D or 3D floor maps, check the asset location by entering its ID, and review performance dashboards and other data.
Pozyx RTLS dashboard
You can also use the RTLS interface to configure your system to do a specific action in response to a certain signal. For example, doors are automatically unlocked when authorized equipment or personnel approaches, or an alert is sent to the forklift driver if there’s an accident risk. Also, you can run analytics algorithms to extract actionable insights from your data.
Often, implementing an RTLS also involves creating a digital twin. It means that you build a virtual replica of your warehouse facility where you can try out possible rearrangement options, run what-if scenarios, and do other simulation experiments – before implementing them in reality. If you’re interested in this technology, check our detailed digital twins overview.
RTLS integrations
Integrating your RTLS with your business management software, be it a warehouse management system (WMS), warehouse execution system (WES), or ERP is crucial to establish a seamless data exchange. Such a connection will allow you to:
- send equipment and personnel ID data to the RTLS to create a database of connected tags;
- send order data to the RTLS so that you can match the task with staff and equipment and build optimal routes; and
- send tracking results to the main system for reporting and analytics, etc.
If you implement an RTLS to automate your inventory management processes, you’ll have to integrate it with your inventory management software (IMS). This way, the systems will exchange information about the SKU ID details, location, production date, etc. For example, car manufacturing giant BMW used to “lose” a lot of produced vehicles somewhere in the storage areas but now, due to their new RTLS, it loses way fewer items.
Such connectivity is developed using APIs. Many RTLS providers that offer turnkey services will build integrations for you. Otherwise, you’ll have to do it yourself either with the help of in-house IT specialists or by engaging external connectivity experts. In this case, check with your RTLS provider if any open APIs are available. Some off-the-shelf products come pre-integrated with major WMS/ERP/IMS solutions which makes things easier. But if you’re using proprietary software, be ready for a full-scale integration project.
RTLS implementation
So how should you approach RTLS implementation? Here are a few recommendations to consider.
Set up a business goal. You have to clearly understand the ultimate objective of your project. For example, do you want to minimize losses from lost or stolen items or speed up operations? In the first case, you need a simpler system that will only visualize the location; while in the second one, opt for a powerful analytics module to perform process mining and uncover inefficiencies.
Calculate expenses. Plunging into the RTLS project, you not only have to pay for hardware (tags, anchors), installation, and software, but also for integration, maintenance, staff training, and much more.
Launch a pilot. Start small. Try out the system with just a few tags and anchors installed in different zones (since the accuracy depends on the environment). Test different technologies and compare them to know which one works best in your case. For example, Sewio offers a complete UWB Wi-Fi kit that can be installed in 60 minutes letting you track 4 objects on an area of 400 sq.m. Once you see that the system delivers value, you can scale it to track more assets and/or add functionality.
Ensure scalability. Some systems can only handle a certain number of tags, plus, if you chose a local server, its storage/processing capabilities are most likely limited too. So, if you plan to scale your RTLS in the future, keep these limitations in mind and think of ways to overcome them, e.g., upgrade your servers or move to the cloud.
Integrate with other systems. As we said, connect your RTLS with other systems for top performance and data sharing.
Conduct staff training. All these sophisticated systems in themselves are useless without the enterprise-wide regular usage. Make sure your employees know how to handle the new devices and software, give access permissions to designated operators, and empower managers to act on the additional information they get from an RTLS.
Engage IoT experts. IoT systems are powerful tools that, just like any other complex structure, require maintenance and fine-tuning. Engage professionals who will assist you with building, connecting, and customizing your RTLS so that you can get maximum value from its implementation.
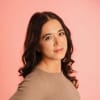
Maria is a curious researcher, passionate about discovering how technologies change the world. She started her career in logistics but has dedicated the last five years to exploring travel tech, large travel businesses, and product management best practices.
Want to write an article for our blog? Read our requirements and guidelines to become a contributor.