In today's fast-moving world, cross-docking connects suppliers, resellers, and customers quickly and efficiently. That’s why it became a preferred shipping method for companies from various industries. Such big brands as Walmart, Toyota, and Lowe’s leverage cross-docking to streamline their operations and cut costs.
But cross-docking will only be beneficial if executed properly – and that takes quite a bit of effort. You have to pay close attention to the facility location and design, install proper equipment, and arrange handling activities – but most importantly, create an optimal schedule and orchestrate the inbound and outbound flow of goods. And that’s where the role of digital technology can’t be understated.
In this article, we describe the cross-docking process and explore the technology's role in it. We'll look at how software can help manage complex tasks and suggest a few tips on how to approach cross-docking. We primarily address this post to resellers and distributors who want to enhance their existing traditional supply chains with cross-docking.
What is cross-docking, and how does it work?
Cross-docking is a logistics process in which products from a supplier or manufacturing plant are distributed directly to a customer or retail reseller with minimal handling and storage time.
Instead of being kept in a warehouse, as the traditional supply chain implies, goods come through one door and then quickly move out through another door to travel to their next destination.
Companies adopt cross-docking to speed up the supply chain process, reduce storage costs, and ensure that products reach customers quickly. It has proved its effectiveness with
- food products, pharmaceuticals, and other perishable items that require fast shipping to avoid spoilage;
- mass consumer goods with stable demand, like apparel, household items, etc.;
- seasonal or promotional goods that have to be distributed as quickly as possible; and
- prepackaged items that don’t require additional handling or quality checks and can be sent directly to the end consumer.
Besides eCommerce businesses and other resellers, cross-docking is often used by organizations that practice the just-in-time inventory management strategy, meaning they receive the exact amount of inventory they need to satisfy demand, with little to no stock retained.
For a better understanding, let’s look at the entire process step by step.
Cross-docking process
As we said, different scenarios of how cross-docking works are possible. Here, we’ll go through the most common one.
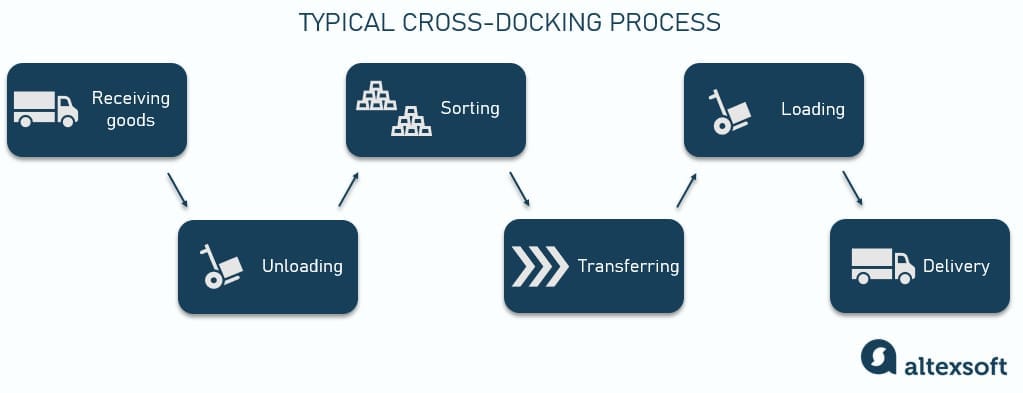
Cross-docking process
Receiving goods. Products arrive at the cross-docking terminal, usually in trucks or rail containers.
Unloading. Goods are quickly unloaded from the incoming vehicles.
Sorting. Once unloaded, the products are sorted in the docking terminal. This sorting is based on their final destinations or the type of product.
If goods come in presorted and ready for immediate transfer with no additional actions required, it’s called transshipment. In other cases, incoming merchandise needs to be reassembled or combined with goods from other suppliers.
Transferring. After sorting, goods are moved from the receiving dock to the outgoing shipping dock via a forklift, conveyor belt, pallet truck, etc. There's no storage in between. The products are simply transferred across the dock (though sometimes they might undergo additional processes such as quality checks, kitting, or packaging). If goods from multiple suppliers are combined into a single truckload, it’s called consolidation.
Please refer to our post about load planning to learn more about how to handle less-than-truckload and consolidated shipments.
Loading for delivery. At the shipping dock, the sorted goods are loaded on trucks or trains.
Ongoing transportation and delivery. Finally, these loaded vehicles depart from the cross-docking terminal to deliver goods to customers, retail stores, or other specified locations.
We mentioned the docking terminal in our description, so let’s take a moment to explain what it is and how it’s different from a traditional warehouse.
Cross-docking terminal
As a rule, cross-docking involves handling goods in a specialized terminal designed for swift movement and redistribution of shipments. Its construction differs from a standard warehouse that’s geared towards storing and managing inventory over a longer period.
Such a facility is usually a long, narrow building with dozens or even hundreds of loading and unloading docks. An I-shaped configuration is most common, while larger ones may use more complex T-shaped or X-shaped configurations. There must also be a convenient drive-in and a spacious yard to efficiently manage incoming and outgoing traffic.
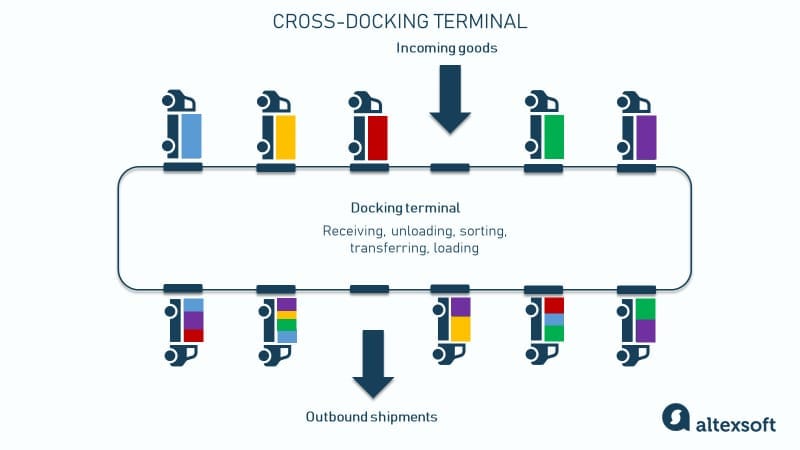
I-shaped cross-docking terminal
However, the transfer of shipments can also be performed in any storage facility, distribution center (DC), staging area, or even by directly reloading from one vehicle to another.
Cross-docking pros and cons
The key reasons companies turn to cross-docking are speeding up delivery and cutting storage, transportation, and labor costs. Its other advantage is reduced risk of spoilage, damage, or theft due to minimal handling.
Meanwhile, there are also a number of drawbacks worth considering if you think about implementing cross-docking. The biggest one is supply chain vulnerability and over-reliance on your suppliers – any disruption can destroy the perfect schedule and ultimately lead to delayed deliveries, stockouts, and unhappy customers.
In addition, cross-docking typically requires significant initial investment as many companies build their own facilities and create vehicle fleets to transport their goods. And even if you outsource transportation to third parties, you still need to set up an advanced IT infrastructure to coordinate the flow of shipments. And that’s what we’re going to talk about next.
The role of digital technology in cross-docking
As we mentioned in the beginning, to be effective, cross-docking requires careful planning and coordination. Manually arranging the incoming and outgoing flow of transportation and goods is too difficult, if possible at all. So digital technology has become a must.
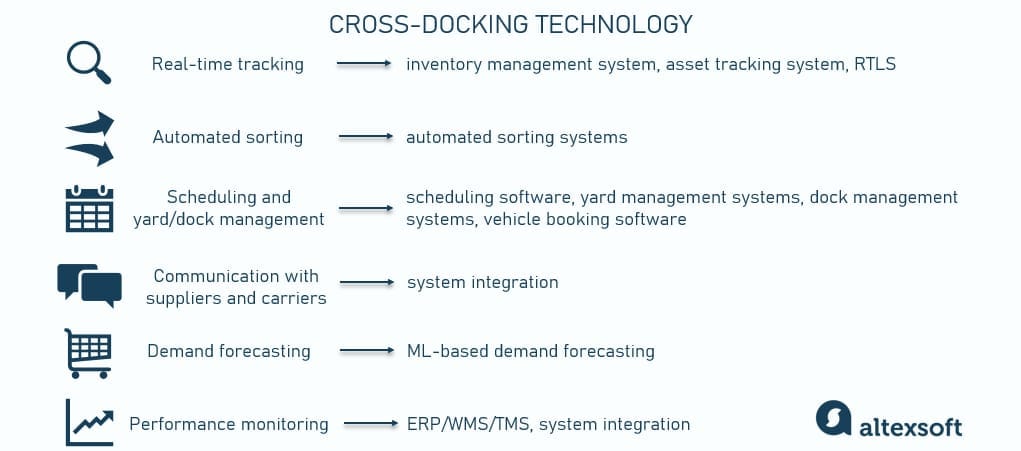
Technology that can support cross-docking workflows
Let’s talk about workflows that software can support and optimize.
Real-time tracking
Business challenges: lack of visibility into incoming inventory and location of items, lengthy and error-prone manual checks
Technological solutions: inventory management system, asset tracking system, RTLS
Cross-docking must be fast. You can't waste time looking for lost shipments and disrupting the entire flow. You have to know what exactly comes into the facility, where all received items are at any given moment, and where they go next.
Tracking systems, often using RFID (Radio-Frequency Identification) and barcoding, allow you to accurately identify inventory, know the location of goods in the cross-docking facility, and speed up handling activities. Staff can track items in the facility by reading RFID chips or barcodes and matching the information to the load lists in the system.
And if you implement an advanced, IoT-based real-time location system (RTLS), it will also help you analyze your operations and suggest ways to optimize them.
Automated sorting
Business challenge: slow, inaccurate sorting processes
Technological solution: automated sorting systems
Sorting is traditionally the most drawn-out and error-prone process due to the need for human intervention. However, today, there are automated sorting systems or sorters to help you out.
They can be semiautomated or fully automated. As shipments move along the conveyor belt, the sorting system automatically scans and identifies them, matches shipping details to those in the database, and sorts freight depending on its type and destination, sending it to the relevant dock.
This requires less staff, reduces manual errors, and speeds up the process, which is vital in a cross-docking environment where time is of the essence.
Scheduling and yard/dock management
Business challenges: inefficient dock/equipment/staff scheduling process, inability to timely react to disruptions
Technological solutions: scheduling software, yard management systems, dock management systems, vehicle booking software
Cross-docking involves the continuous flow of incoming and outgoing vehicles. These flows must be synchronized to minimize wait times, maximize turnaround, and optimize dock usage. Dock/yard management software helps schedule dock appointments, coordinate staff and handling equipment, and efficiently manage the yard space. The vehicle booking system (also called the truck appointment system) allows suppliers and carriers to self-book available time slots and streamlines gate operations.
Communication with suppliers and carriers
Business challenge: poor information exchange that slows down operations and impedes schedule alignment
Technological solution: system integration
Cross-docking is too complex of a process to be managed via phone calls or emails. Its efficiency largely depends on continuous, seamless communication between all the parties involved.
A solution here can be to interconnect your business management system with those of your suppliers and transportation partners. This way, all the parties will be timely informed about shipment statuses, changes in schedules, order details, and other critical updates. Such system integration also enables an easier exchange of documents.
Demand forecasting
Business challenge: stockouts or overstocking because of inaccurate demand forecasting
Technological solution: ML-based demand forecasting
As we touched on earlier, cross-docking works well with staples that have stable, predictable demand. However, even these products have demand fluctuations – that you have to predict and take into account when planning deliveries. And if you want to execute the cross-docking method to transport goods with unstable demand patterns, you must implement an advanced demand forecasting system to stay out of trouble.
If you need more details, please visit our overview of demand forecasting and the role of machine learning in it or watch the video below.
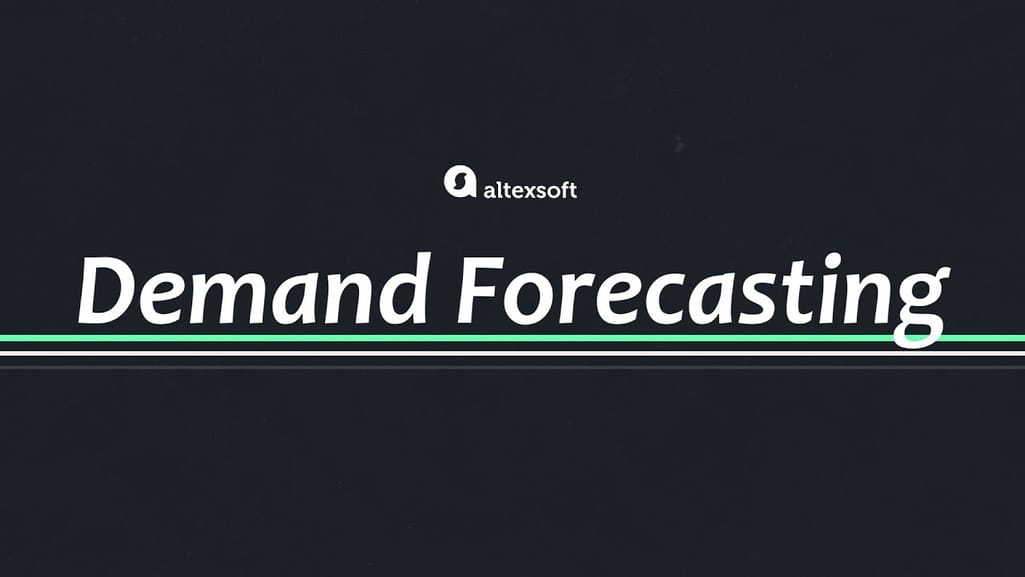
How to approach demand forecasting
Performance monitoring
Business challenges: lack of understanding how business performs, inability to identify bottlenecks and optimization opportunities
Technological solutions: ERP/WMS/TMS, system integration
To manage your supply chain effectively, you need to understand how every part of it performs. A comprehensive ERP or other business management platform will allow you to get a clearer picture of your operations.
If you have multiple tools to manage your activities, you'll have to interconnect them to establish better data flow. Having all operational data in a single system will enable you to generate actionable reports, monitor KPIs, see inefficiencies, benchmark your performance, and conduct further analytical procedures. You’ll get visibility not only into inventory or transportation-related processes but also into other operational activities such as supplier management, customer relationships, finance, etc.
How to start with cross-docking
As we said, there are multiple scenarios for implementing cross-docking in your supply chain. For example, you can simply find a third-party logistics service provider or 3PL that specializes in cross-docking and just outsource your transportation activities altogether. In this case, you don’t have to bother about how it works – you only manage your suppliers, process orders, and do the administrative job.
While terms of cooperation can vary greatly, besides delivery, 3PLs are often also responsible for other workflows, i.e., handling returns, customer support, customs brokerage, technology services, etc.
However, if you’re a growing wholesale, retail, eCommerce, or manufacturing business that wants to add cross-docking to the existing supply chain, here’s what you can start with.
Physical setup
First, look at the facilities and equipment you’re already using.
Warehouse layout. Review your current warehouse layout and reorganize your space so that you have the sorting and staging areas near the docks – the closer the better. You need to have enough room for your activities to avoid congestion and prevent any safety risks. Remember to keep them clutter-free at all times.
If you decide to scale your cross-docking operations, you’ll have to build or rent specialized docking terminals we described earlier.
Yard space. Cross-docking often implies dealing with active incoming and outgoing traffic. Make sure you have enough parking spots in your yard and enough space for trucks to move around so that they don’t get stuck and slow you down.
Equipment. If you have a continuous, big volume flow of goods, use a conveyor belt to speed up your sorting and transferring operations. As you scale, consider implementing an automated sorting system.
Operations
Cross-docking workflows are different from traditional warehousing ones, so you’ll have to adapt how you operate.
Workflows. Design the new workflows and train your staff. Depending on how your existing supply chain works, you might get away with a simple transshipment or need more complex processes like consolidation, packaging, kitting, etc.
Schedules. Develop schedules to coordinate the flow of goods. Make sure all parties (suppliers, staff, carriers) understand how important sticking to them is. Set up an appointment system where suppliers and carriers can see and book time slots.
Technology
Most probably, you already have a business management solution in use to automate your operations. While there’s no specialized software focused on cross-docking only, the good news is that many supply chain management (SCM) platforms support this process.
Management system. Assess your ERP/SCM/WMS/TMS and see if it includes the functionality we mentioned above, i.e., dock scheduling, asset tracking, demand forecasting, etc. Many off-the-shelf supply chain software tools support a range of diverse workflows and sometimes have a cross-docking module. But even if they don’t, it might turn out that the platform you operate on is enough for a start.
For example, a warehouse management system (WMS) helps manage all kinds of warehouse operations, such as receiving and sorting processes, ensuring that incoming goods are quickly identified, reassembled if needed, and dispatched. WMSs also help optimize space usage in the terminal.
If you operate your own fleet of trucks, you probably use a transportation management system (TMS) to build transportation schedules and routes. This software ensures that incoming and outgoing vehicles are coordinated efficiently by sending drivers notifications when and to which gates/docks they have to drive up. TMSs also help create shipping documentation, manage carriers you work with, and control transportation costs.
An inventory/order management system allows you to track inventory and process orders, minimizing inaccuracies and lost items. It also helps manage paperwork and relationships with your partners.
See Also
Additional tools. As you assess your existing system, you might feel you need additional functionality to automate certain workflows. Define your needs and implement focused tools (for example, a vehicle booking system or a dock scheduler).
Integrations. Remember to connect all your digital systems is a single IT infrastructure and establish a smooth data flow. If you add focused tools, check their list of pre-integrated partners, as many of such solutions already have a built-in connection with other industry platforms. If that's not the case, you'll have to engage internal or external IT specialists to build such an integration.
Also, see if it’s possible to connect to the systems of your suppliers and carriers to streamline your communication and information exchange.
End-to-end visibility and analytics. As you grow, you will likely need a more sophisticated system to get better supply chain visibility, analyze your performance, and optimize existing workflows. Consider developing an infrastructure for data collection, storage, and processing. Implementing machine learning techniques will allow you to improve the accuracy of demand forecasting and analytics processes.
To sum up, cross-docking can become a great enhancement for your supply chain, but it's definitely not the easiest venture. Setting it up properly will require a lot of effort and investment. A good practice is to start off with one SKU (stock keeping unit) or, say, a product group from one supplier and see how it goes. As you test and improve your workflows, you can then gradually scale them to other inventory, advance your technologies, optimize operations – and reap the benefits.
For additional inspiration, here are a few examples of how companies from different industries implemented cross-docking.
Cross-docking real-world examples
The world’s largest retailer, Walmart is one of the iconic examples of using a cross-docking approach. It has 210 distribution centers of over 1 million square feet in size each serviced by 600+ personnel unloading and shipping over 200 trailers daily. Facilities are strategically located so that each DC supports 90 to 100 stores in a 150+ mile radius.
As for technology, Walmart implemented Symbotic System in its regional DCs. This end-to-end automation technology platform powered by autonomous robots and AI allowed the retailer to automate sorting, tracking, retrieving, packing, and even load planning. As a result of such a supply chain setup, Walmart was able to streamline its cross-docking workflows, reduce shipping time and cost, and arrange same-day delivery to stores and customers.
Amazon, another leading retailer, also has a network of Inbound Cross Dock (IXD) facilities located near all major ports. There, overseas import containers incoming from foreign vendors are received, sorted, consolidated, and loaded on trucks to be transported to the fulfillment center network.
Amazon also operates IXD facilities in Europe like the one in Dortmund, Germany, with diverse automation technologies in place, including
- 13 km of conveyors,
- 4 fully automated systems for package identification,
- 203 workstations for receiving goods, and
- 360-degree robot arms to handle various tasks.
Lowe’s, a North American home improvement retailer, also uses a cross-docking approach to meet the growing need for faster delivery. In 2020, the company shared its plans of expanding its supply chain with additional 50 cross-dock delivery terminals (among other facilities). These terminals are to be operated with the existing WMS, to provide visibility throughout the distribution network. This expansion aimed at providing same-day and next-day fulfillment options to Lowe’s customers.
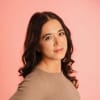
Maria is a curious researcher, passionate about discovering how technologies change the world. She started her career in logistics but has dedicated the last five years to exploring travel tech, large travel businesses, and product management best practices.
Want to write an article for our blog? Read our requirements and guidelines to become a contributor.