Turmoil and disruptions are constant companions of cargo terminal operations. Delayed ships, queued trucks, heaped containers – all this mess is totally inevitable… or is it? Actually, introducing some order into this world of chaos is more than possible. We’re going to explore how vehicle booking technology can streamline cargo facility operations and smooth out the peaks and troughs of terminal activity.
What is a vehicle booking system?
A vehicle booking system (sometimes called truck appointment system) or VBS is a piece of software that allows terminal operators to schedule the arrival and movement of vehicles in the terminal.
Why implement a VBS?
Its main purposes are:
- to optimally arrange the loading and dropping of shipping containers,
- to improve internal asset utilization,
- to avoid congestion,
- to increase throughput capacity,
- to decrease emissions, and
- to improve security.
In this sense, a VBS has a lot in common with a yard management system that is applied for the same purposes but in a different setting.
On the other hand, hauling companies and truck drivers also benefit from the use of a VBS since such a scheduling system allows them to better plan their own operations and avoid wasting time and fuel while idling in line in front of the terminal gate.
Where is VBS used?
A VBS is usually implemented at sea container terminals to support maritime logistics, but intermodal/railroad freight transportation facilities can also put it to good use.
Where to get a VBS?
There are some providers of the ready-made VBSs that can be used in a container terminal such as Camco, Visy, or 1-Stop. However, to achieve maximum customization, many modern cargo facilities develop a bespoke solution that meets their specific business needs.
How does a VBS work?
Here, we illustrate and briefly describe the common usage of the VBS in a port cargo terminal.
How a VBS is used
Registration. The hauling company registers with the VBS portal to get access to the scheduling functionality. Registration is usually free and involves the submission of the application form with company information and direct debit mandate.
Scheduling. When there’s a need to enter the terminal, the carrier books an available time slot in advance (typically 24 hours or more), submitting the vehicle information and associated container details. Without such an appointment, automated ports/terminals will not let vehicles in the facility.
Arrival and verification. Once the vehicle arrives, the gate staff or automated system validates the vehicle details against pre-registered ones. Some systems verify the driver as well through ID scanning or biometrics check.
Loading/unloading. The vehicle proceeds to the corresponding berth/warehouse/container depot to load or unload freight.
Billing. The carrier is charged for booked appointments. Typically, invoices are issued on a monthly basis.
As you can see, a VBS not only helps with scheduling and managing incoming and outgoing traffic, but also contributes to other processes, i.e., gate operations, billing, data collection, and so on. Let’s look closer at the main VBS features that help expedite and optimize terminal activity.
VBS main features
Ok, so which VBS functionality allows terminals to eliminate time-consuming, error prone paperwork and manual operations and tackle the everyday bedlam?
Scheduling
As we mentioned above, arranging appointments is the primary function of a VBS. The system has to generate time slots according to predefined business rules for a predefined number of trucks (these rules and numbers depend on the specific terminal’s capacity and handling resources). A VBS constantly updates available capacity so that no overbooking happens in peak times.
Instead of emails or phone calls, carriers can calculate their ETA and book a convenient slot.
Visy VBS booking interface
When the booking is created and confirmed, carriers might need to export it to various formats or print it out. They might also want SMS or email instructions on passing the gate to be sent directly to drivers.
Such self-scheduling is dynamic, allowing drivers to readjust their appointment in case of delays or other changes. Business rules in different terminals might vary, sometimes not allowing for late rescheduling or canceling the appointment automatically if no container details are provided.
If you operate multiple terminals, consider providing carriers the opportunity to create multi-terminal bookings to be able to deliver or collect cargo in several facilities during the same visit.
Also, a multi-format importing functionality will be useful for carriers who work with many containers so that they can easily transfer freight details (container number, export/import, seal/PIN number, etc.) to your VBS from their internal system.
Gate management
Accurate scheduling helps solve congestion problems both at the landside and the terminal gate.
Verification and administration processes at truck gates can take forever if done manually. However, when all the essential vehicle, driver, and container information is pre-registered, gate staff or automated security systems can quickly identify and verify vehicles and prevent bottlenecks, allowing trucks to efficiently go in and out of the terminal.
Fully automated systems are equipped with cameras that detect the vehicle details (some additionally require the driver to enter the pre-issued PIN-code, scan his/her ID, or pass the biometrics check). We’ll talk more about such solutions in the next section.
Billing
A carrier’s interaction with a VBS to book appointments is a billable activity that has to be accurately captured. Charges depend on the time and day, as well as a number of other criteria.
For example, many terminals such as the Port of Felixstowe charge an extra fee for peak hours, while some (e.g., Port of Southampton) have additional charges for old license plates (green charge) or passengers in the cab. Usually, charges also apply if the hauler doesn’t show up at the appointed time.
All these activities have to be recorded, added to the total invoice, and sent to the carrier. As we said, typically it’s performed once a month.
Data collection and analysis
Data analytics is an important business process for any organization. Information collected by a VBS can be a valuable source of insights and provide overall understanding of facility performance. You can track
- gate metrics (number of arrivals, types of freight, types of incoming vehicles, waiting time, etc.),
- carrier metrics (number of bookings per carrier, number of used/rescheduled/canceled bookings, number of no-shows, etc.),
- financial results, and so on.
Knowing these operational indicators and combining them with other facility metrics, terminal operators and managers can get fuller visibility, understand gate capacity and traffic patterns, and make informed decisions on their landside activities, asset utilization, further modernization and investment, and so on.
Additional features
If you're thinking about developing a custom product, consider adding more functionality to your VBS.
Different terminals have different security requirements. Contemplate using a VBS to inform drivers about your facility safety and security procedures, provide maps and instructions, and add a test to verify rules understanding and compliance. As an example, check DP Southampton Driver Awareness Assessment page.
An in-built communication channel or at least a chatbot will facilitate interactions between carriers and terminal staff (operators or customer service).
Providing carriers access to vessel schedules and container availability will greatly assist them with scheduling their appointments. Consider creating a search interface and an online information board about ship arrivals and status.
Port of Houston container search interface
Automated notifications of updated container status, weather changes, ship delays, or lagged custom clearance procedures will allow carriers to schedule (or reschedule) their visits in a timely manner and avoid “empty trips” or wasting time waiting for associated freight.
Registering with APM Terminals allows carriers to receive terminal alerts and create a personal watchlist to receive container status notifications
Developing a linked mobile app for carriers will allow drivers to manage their bookings from smartphones.
Whether you choose to buy an off-the-shelf VBS or build your own platform, there’s one more crucial aspect you’ll have to take care of – connectivity.
VBS integrations
Integrating software in your existing IT ecosystem is essential for proper automation and seamless data exchange. You might be using different types of business solutions in your operations, so here are some integration options for you to consider.
VBS integrations and data exchange
Terminal operating system. TOS is the main piece of software used to manage all terminal operations, from equipment and staff scheduling to cargo sorting to accounting. Connecting the VBS to the TOS is vital to streamline container drop-off and pick-up activities and exchange information on incoming and outgoing vehicles and cargo.
As a result of such integration, for example, turnaround time can be greatly reduced by pre-planning the container position (e.g., if the carrier books the earliest time slot for pick-up, the container will be placed at the top of the stack or in a way that grants easy access).
The work of cranes, forklifts, and other landside equipment that’s managed in the TOS can be arranged according to the VBS schedule.
Also, connecting the VBS to the TOS will allow for receiving incoming vessel information and container status to enable more accurate appointment scheduling. Sharing details about cargo allocation (berth, warehouse, dock number, etc.) will support orientation in the facility.
Carriers can see the container status from the DP Southampton VBS watchlist
Gate operation system (gate automation system). GOS typically consists of self-service kiosks, OCR cameras, RFID scanners, automated security barriers, intercom devices, information displays, and specialized software to bind it all together. Some of these elements can also come as separate automation solutions.
If you use a standalone GOS, you’ll have to integrate it with the VBS so that the driver, vehicle, and container details can be easily shared and verified. Plus, the GOS sends the data on incoming vehicles to the VBS to enable tracking of scheduled arrivals and no-shows.
Security kiosks. Multilingual self-service kiosks automate gate processes and, when integrated with the VBS, allow for quick vehicle registration and verification. In addition, such portals can be installed at the berths or warehouses to reconfirm the loading or drop-off.
OCR (оptical character recognition) software. OCR technology scans all the incoming and outgoing vehicles and automatically detects such information as:
- container numbers,
- ISO codes,
- trailer numbers,
- license plates,
- chassis numbers,
- IMDG dangerous goods labels,
- door direction,
- container position on chassis, and
- container state (full or empty).
Integration with OCR portals facilitates vehicle verification and enables efficient gate management.
Accounting software. For accurate billing, data from a VBS has to be carefully transferred to the accounting system.
Carrier’s system. A carrier might want to integrate with your VBS to be able to receive available time slot information and schedule appointments from their own interface. That would require developing a set of APIs that your partners can connect to.
You can see that building a robust system that will be effective and actually optimize your terminal operations can be quite bothersome. Here are a few inspirational examples that prove that the result is worth the effort.
VBS implementation success stories
Today, multiple container terminals around the world have already adopted a vehicle booking system that allows them (and haulers too!) to increase their efficiency and gain other benefits.
Due to the VBS implementation in all four major ports around Australia, these major efficiency improvements were realized.
- Dwell time decreased from 5 to 2.8 days.
- Terminal capacity increased from 800,000 TEU to 1.1 million TEU.
- Truck turn time decreased from 81 to 25 minutes.
- Unproductive yard shifts decreased by 4000 per month.
The Belgian Antwerp Gateway Terminal adopted a VBS to address truck congestion. They also created “virtual buffer” queues and used a call-up principle. So, drivers wait for their turn remotely, monitoring the queue on the visual board, and get notifications when they can enter the facility. As a result, truck lines were eliminated and CO2 emissions reduced by 730,000 kg within the first year.
Los Angeles and Long Beach, housing some of the busiest U.S. port terminals, made a step towards automation and started demanding haulers to make appointments in 2019. In December 2019, the turn times of automated terminals got to the lowest point since 2014 (30 and 35 minutes in different facilities), while the turn times for the manual terminals ranged from 52 to 92 minutes.
Implementing the truck appointments systems in two international terminals in Manila, Philippines, helped increase container throughput by 55 percent and allowed haulers to run twice as many trucks as before.
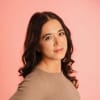
Maria is a curious researcher, passionate about discovering how technologies change the world. She started her career in logistics but has dedicated the last five years to exploring travel tech, large travel businesses, and product management best practices.
Want to write an article for our blog? Read our requirements and guidelines to become a contributor.