The COVID-19 pandemic demonstrated to us how vulnerable supply chains can be and how important it is to manage them closely. In this article, we’ll talk about supply chain management, discuss its key components, and explore some recognized software tools that can increase your efficiency and resilience.
What is supply chain management (SCM)?
Supply chain management (SCM) is the process of planning, implementing, and controlling the operations of a supply chain for the purpose of satisfying customer requirements as efficiently as possible. Supply chain management spans all movement and storage of raw materials, work-in-process inventory, and finished goods from the point of origin to the point of consumption.
This definition was suggested by Keith Oliver, a leading British logistician who first mentioned this concept in an interview with the Financial Times in 1982. Since then, multiple experts have offered their own definitions of SCM. But in a nutshell, it can be described as supervising the whole flow of goods and services, from raw materials to final products.
Now, let’s break this massive concept into pieces.
Supply chain management process
Obviously, managing supply chains involves a multitude of diverse activities that can be categorized into several main groups.
Supply chain management main activities
Planning relates to predicting future demand and building a corresponding strategy for every department, i.e., sourcing materials, scheduling staff, arranging transportation, and so on. It’s a crucial stage that has to be based on comprehensive market information and analytics to make accurate forecasts.
Procurement is about purchasing the right amount of the right materials at the optimal price. It’s also about choosing suppliers and maintaining business relationships.
Manufacturing is transforming raw materials into end products with the help of human labor, equipment, and sometimes other external factors. Some businesses that deal with ready-made goods or services (like eCommerce or retail) don’t have this stage as part of their supply chains.
Distribution and logistics is about finding customers, making deals, arranging storage and transportation, and delivering goods. It also involves dealing with returns.
Inventory management aims at controlling stock assortment and level throughout your supply chain.
Analytics is a throughline that goes across all stages and helps control supply chain performance, find areas for improvement, and make decisions.
We’ll talk more about each of these stages further on, and now, let’s briefly clear up a few more concepts that are closely related to supply chain management.
Operations and supply chain management
SCM is tightly interwoven with operations management (OM), which focuses on coordinating and optimizing internal processes, whether it be designing and manufacturing goods or developing services. To put it simply, both SCM and OM take care of the same product but at different stages of its lifecycle.
There are several areas where SCM and OM functions can overlap. But basically, SCM is in charge of outside interactions with suppliers, warehouses, distributors, and end-customers, while OM supervises everything that happens inside the company.
Operations management vs supply chain management
Small companies often don’t separate the external and internal parts of product flow so that the same specialist or department controls all phases goods and services go through en route to the end customer. Large organizations usually split responsibilities between two executives — a supply chain manager and an operations manager.
Supply chain manager and operations manager roles
The top objective of both experts is to save expenses and boost production efficiency without compromising on quality. But while a supply chain manager focuses on external processes, an operations manager solves pressing internal tasks. The former negotiates terms with third-party contractors (suppliers, logistics teams, distributors) and optimizes the movement of materials and goods from one point to another outside the organization. The latter communicates with stakeholders and implements policies to boost manufacturing and get things working well inside the company.
Given that both pursue the same global goal and work on the same product, they have some overlapping responsibilities. For example, both are involved in:
- price forecasting, overseeing budgeting, planning, and auditing;
- cost management (estimating, controlling, optimizing, and reducing operating costs);
- inventory management to ensure effective stock utilization and reduce warehousing costs; and
- demand forecasting, crucial for preventing overproduction and oversupply.
Efficient supply chain and operations management can help build what is called a resilient supply chain. Let’s say a few words about it as well.
Supply chain resilience
Supply chain resilience is basically its ability to recover from disruptions. Moreover, a resilient supply chain is able to adapt to the changing environment and readily develop new strategies to mitigate anticipated risks.
This concept originated in the discipline of risk management – which is incredibly important in the supply chain world where disruptions are a regular occurrence. Anything from a truck breakdown or paperwork mistake to a hurricane or pandemic can cause a seemingly well-oiled system to stop functioning. A 2021 Association for Supply Chain Management disruption report states that 85 percent of organizations have experienced significant disruptions resulting from the COVID-19 pandemic that they haven’t recovered from yet.
That’s why supply chain resilience should become the main focus of the supply chain management strategy. It’s crucial to discover vulnerabilities and address them, for example, by carefully choosing your suppliers and diversifying your partner portfolio or using multiple carriers to safeguard your delivery activities.
Transparency across all supply chain operations and data analytics is vital for enhancing resilience. Modern technologies help scrutinize data from multiple internal and external sources, spotting trends and defining opportunities. That allows supply chain managers to not only timely react to disruptions but also to predict them and take proactive measures.
Today, technology can help automate and streamline all supply chain processes. So, let’s look closer at what exactly can be done.
Digitizing supply chain management operations
Enhancing your supply chain with modern digital solutions will allow you to improve your operations and increase efficiency. Let’s see how technology can transform every single aspect of any supply chain.
A brief overview of the main supply chain management modules
Planning
Demand planning initiates and drives operations in all segments of a supply chain, from purchasing raw materials to product distribution.
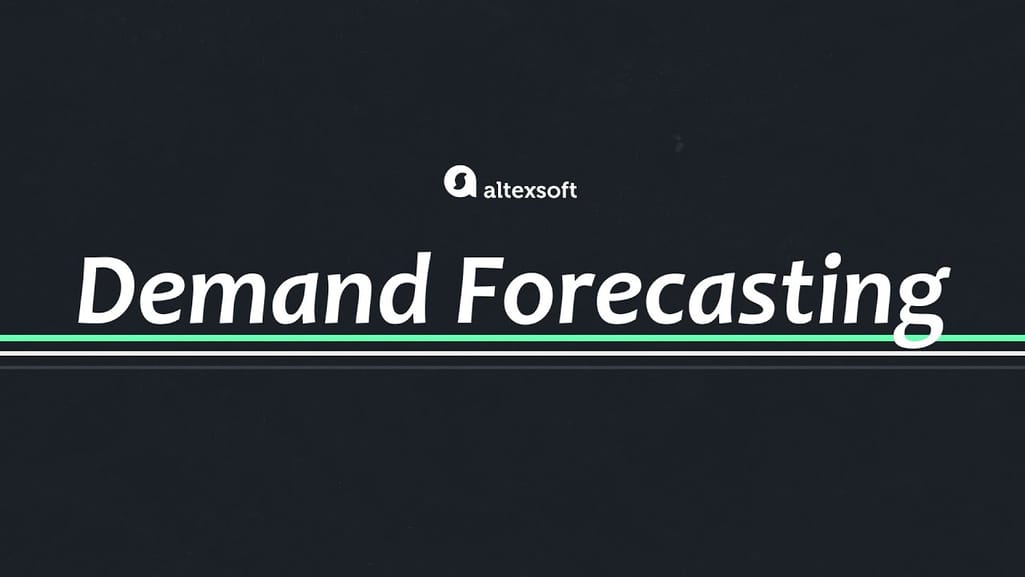
Watch how predictive analytics helps with demand forecasting
In many organizations, the planning processes still rely on tricky and rigid spreadsheets, unable to reflect and accurately predict demand volatility. Thus, the implementation of modern demand forecasting software can give you a huge competitive advantage, bringing transparency and reliability into predictions.
Accurate, timely forecasting of customer requirements helps businesses achieve the following goals:
- timely procurement planning and negotiating better purchase terms,
- improved capacity utilization,
- elimination of production delays,
- enhanced customer satisfaction, and
- minimizing the so-called bullwhip effect — a situation when a small rise in product demand leads to excess inventory across the whole supply chain, with gradual enlargement as the information about sales growth travels back from a consumer to a raw materials vendor.
We’ve already discussed how retailers apply artificial intelligence. But what digital capabilities are particularly useful for improving demand forecasting? Here are some features worth considering.
Demand sensing. A demand planning system aggregates large volumes of real-time data from multiple sources to identify demand trends and generate accurate short-term forecasts. This enables quick reaction when unexpected changes occur.
Demand segmentation and modeling. AI-powered software can optimize forecasts for different channels, products, customers, and more. Moreover, you can simulate multiple demand scenarios and analyze consumer buying patterns to make more informed decisions.
Resource planning. Based on demand forecasting, the software makes suggestions on the volumes of resources required to meet customer needs.
Collaborative forecasting. Suppliers, partners, and stakeholders can be brought into planning for collaborative forecasting.
New product forecasting. The system analyzes the sales history of similar products, considers different factors (like season, launch time, or region), and applies complex models to predict demand for new goods or services.
This list can be continued and extended as new technologies are emerging all the time, penetrating deeper into complex processes and simplifying them.
Procurement
Procurement, or obtaining materials, goods, and services you need to run your business, is the very first element of a supply chain.
The procurement cycle involves multiple steps — analyzing and selecting vendors, negotiating terms, ordering, and invoicing, to name a few. A significant part of these procedures can be delegated to procurement management software. This will speed up the workflow, enhance transparency, save time, and, finally, reduce costs, which is a key priority for 78 percent of procurement leaders.
The core functionality of procurement software covers the following areas.
E-sourcing. Before buying materials or goods to run your business, it’s vital to collect, check, and compare information about different vendors to choose the best one. E-sourcing automates several steps of the traditional sourcing routine.
Preliminary data collection. The system sends a standard electronic prepurchase questionnaire (PPQ) and a request for quotation (RFQ) to each potential vendor. After filling in the forms, vendors upload their answers into software, giving procurement managers instant access to all the information.
Automated evaluation. At all stages of procurement, e-sourcing solutions use analytical tools to sort through documents sent by suppliers, draw and process essential information, verify compliance of a vendor with business requirements, compare prices and other metrics, and highlight unsuitable proposals. The results can be displayed on the dashboard as informative data visualizations.
Invitation to tender (ITT). Vendors sorted out for the next stage of sourcing automatically receive invitations to tender forms that specify the requirements of the organization and details of the evaluation process.
E-auction. Vendors are invited to tender and submit their bids to the shared platform. All parties involved have access to all bids and compare offers, which prompts suppliers to reduce prices.
Contract management. Among other things, the digital "administrator" helps you create and standardize contract templates, boosts approval processes, and captures electronic signatures.
Procure-to-pay (P2P) operations management. P2P is a subdivision of procurement that covers financial transactions. The set of P2P features differs from product to product. But the core functionality usually boils down to managing a purchase requisition process, generating and tracking purchase orders (POs), and invoice matching. The system compares invoices to the corresponding POs to eliminate mistakes and duplications. If there are any deviations, the invoices are sent back to the supplier for corrections. Otherwise, payment is authorized.
Vendor (supplier) management. An app aggregates all data about your vendors, updates it, and alerts you about expired qualifications and assessments. The performance of suppliers is measured against critical metrics such as speed, accuracy, quality, and price.
A VMS dashboard gives you a big picture of all supplier-related data and activities. Source: datapine
Spend analytics. The automated collecting, classifying, and analyzing of expenditure data brings visibility to the complex procurement process and allows businesses to discover savings opportunities.
You can read more about procurement analytics in our dedicated post.
Manufacturing
The manufacturing industry has always strongly relied on physical equipment, but as the world changes, digital technologies have paved their way into production as well. Manufacturing software solutions help bring visibility into operations, discover bottlenecks, and minimize downtime. Here are some of its features.
Production scheduling and resource allocation. As you receive production orders, the system can automatically create manufacturing orders and work orders according to available workstations, resources, and staff.
BOM management. A bill of materials (BOM) is one of the main documents in manufacturing. In a nutshell, it’s a full list of used parts and materials – and it can be very long. Manual BOM creation is too error-prone, but software can allow you to easily generate accurate BOMs, manage your components, and control costs.
OpenBOM tool
Automated product inspections. Computer vision systems enhance and automate quality control processes, not to mention speeding them up immensely. Made on the basis of deep learning technologies, they had great results in detecting defects, damages, invalid/missing labels, and so on – while saving time and money.
Condition monitoring. You can see the health status of your equipment in a single system via a network of connected sensors and Internet of Things (IoT) devices and get alerts in case anomalies are detected.
Predictive maintenance. Advanced analytical software can support predictive maintenance. In this case, a sensor-based IoT infrastructure is created to collect measurements from machinery, analyze them, and predict failures so that repairs can be precisely scheduled to reduce downtime and minimize operational disruptions.
Production analytics. Once you have all the information in one system, the software can assist with monitoring equipment performance, analyzing costs and production cycles, and making other essential assessments.
To learn more about AI usage in manufacturing, check our recent post as we move on to logistics.
Distribution and logistics
Logistics is a huge part of SCM that bridges production and sales. It covers all processes that refer to customer relationships and the movement of products and information between a manufacturer/seller and consumers — namely
- marketing activities,
- processing orders,
- warehousing,
- integration with shipment carriers,
- transportation management,
- reverse logistics,
- customer relationship management,
- logistics analytics, and others.
The primary goal for logistics efforts is to meet customer needs in the shortest time and at the lowest cost possible. And that’s where smart technologies play a crucial role.
To learn more about digital transformations in the field, read our in-depth overview of logistics management systems (LMS) and their main modules.
Inventory management
Inventory can be defined as all goods and materials a company keeps on hand to meet customer demand. There are four major categories of inventory:
- raw materials;
- work-in-process (WIP), or components, assemblies, and partially finished goods waiting for completion;
- finished/packaged goods; and
- maintenance, repair, and operating (MRO) items necessary to support and maintain a production process. This category spans all goods that keep business operations running, from industrial equipment and computers to uniforms and office supplies.
Source: APICS Coach
In an ideal world, the first three categories of items would move through the supply chain without stops and bottlenecks, ensuring a rapid investment payback. In reality, supply is rarely (or rather never) equal to demand, with inventory expenses amounting to a substantial 45-90 percent of the company’s total budget. The cost of excess stock can be huge, tying up company funds and reducing cash flow.
Inventory control aims at finding and maintaining the perfect balance between holding too much stock and running out of it across all supply chain nodes. This complex task requires the coordinated effort of different departments. As the business grows, it becomes harder to manage multiple separate subdivisions manually.
The adoption of specialized systems can help you integrate numerous inventory points under one umbrella for more effective, centralized administration. While the choice of available solutions is wide, the common set of must-have features for inventory management software looks like this.
Multi-location inventory tracking. The software allows for organizing and tracking inventory items by suppliers, serial numbers, tags, barcodes, SKUs (stock keeping units or a number assigned to a product to track inventory), or other IDs at different location levels (bins, shelves, racks, aisles) across multiple warehouses. You can easily find a specific part or product, monitor locations, trace item transitions, view overstocks and stockouts.
Low inventory alerts. They appear in your dashboard when the quantity of certain items reaches the preset low limit.
Automated replenishment. In the case of frequent reorders, a replenishment tool can automatically create purchase orders and send them to vendors.
Digital FIFO tools. FIFO stands for first-in, first-out and describes the principle that the oldest inventory should be used or sold first. This approach leads to the timely identification of obsolete or slow-moving stock.
Barcoding. It involves both software and hardware (scanners and label printers) for assigning, scanning, and managing barcodes. Barcoding solutions bring ease, speed, and accuracy to your inventory operations, such as stock-taking and verification.
Inventory optimization and performance analysis. The system automatically analyzes inventory data (such as sales history) and makes suggestions on replenishment dates and quantities. It also identifies the best-performing products as well as ones with low profitability, indicating where you make the most profit and which products face zero demand.
Real-time reporting. High-end solutions constantly process different metrics and generate visual reports on current inventory levels and turnovers, strengths, and weak points.
An inventory management analytical dashboard maximizes comprehension of the inventory data and trends. Source: CEPRo
Analytics
You might have noticed that we mentioned analytics and reporting in every section. As we’ve already explained, that’s because today, data and accurate, holistic analysis is the key to effective decision-making and, ultimately, success.
Analytically mature companies leverage data science and implement machine learning techniques to benefit from predictive and prescriptive analytics at different stages of the supply chain. From demand planning to controlling transportation conditions to price optimization to overall performance monitoring – data can guide all your activities.
We have a very detailed overview of the role of analytics in supply chains that describes its benefits and gives handy implementation tips.
Supply chain management systems overview
Supply chain management systems are designed to coordinate the entire flow of products (or at least a substantial part of it). Sometimes SCM systems include functions of Enterprise Resource Planning (ERP) software that optimizes internal tasks and processes relevant to the operations management field. Vice versa, ERP suites often contain SCM tools, and their functionality can be expanded by implementing compatible SCM add-ons.
To be more specific, let’s take a quick look at the offerings from top SCM software vendors that lead the pack in terms of revenue and market share. All of them follow the current trend and focus on intelligent, AI-based applications and sustainability.
SCM systems comparison
SAP Digital Supply Chain (SAP SCM): the leading ERP platform for enterprises
One of the world’s oldest and largest software companies, Germany-based SAP has been on the market since 1972. It holds a leading position as a developer of robust ERP systems, with 90 percent of Fortune 500 companies using SAP software for their business needs. The latest and most renowned SAP S/4HANA ERP suite offers components that efficiently solve SCM issues.
During the past few years, SAP has been placing more focus on its SCM solutions, which are marketed under the name Digital Supply Chain. The innovative software products built on top of the SAP Leonardo intelligent platform employ ML and IoT to bring visibility, forecasting, analytics, and collaboration to the next level.
The Digital Supply Chain portfolio includes the following products.
- Supply Chain Planning harnesses capabilities of several other SAP products such as Analytics Cloud, Qualtrics, the first experience management (XM) software to anticipate customer behavior, and the Ariba Supply Chain Collaboration tool to share real-time information with partners and suppliers.
- Supply Chain Logistics helps efficiently handle warehousing and delivery-related operations, including yard management, order fulfillment, tracking, and more.
- The Manufacturing module enables production management, planning, and optimization, as well as quality control.
- Product Lifecycle Management supports the product development process, cost analysis, portfolio management, etc.
- Enterprise Asset Management helps to control and optimize asset performance, plus supports maintenance activities.
Who can benefit from it? SAP products fit exactly into the requirements of large enterprises with thousands of employees and multimillion-dollar budgets. For midsize businesses and doubly so for small companies, their suites are too costly to acquire, implement, and maintain. With SAP SCM, you’ll need a dedicated team of tech-savvy experts to administer the system. And that adds to the total cost of ownership.
Oracle SCM: a flexible system to enhance connectivity and resilience
Founded in 1977 in California, Oracle is known as a pioneer in database management system development and marketing. Currently, the company is also among the top vendors of enterprise software, offering multiple lines of business solutions. Its SCM suite includes the following components:
- Supply Chain Planning — offering demand management, sales and operations planning, supply planning, and collaboration functionality;
- Procurement — with sourcing, contracting, procure-to-pay, and supplier management features;
- Inventory Management — providing end-to-end visibility into item flows and their costs;
- Manufacturing – an integrated manufacturing execution system for different production flows;
- Maintenance – supporting preventive and predictive servicing, asset management, repairs scheduling and execution control, etc.;
- Order management — consolidating orders and invoices from all channels and orchestrating order-to-cash operations; and
- Logistics — integrating transportation, warehouse, and global trade management systems. The module covers a wide range of tasks, from shipping optimization to regulatory compliance, for a seamless international trade experience.
In addition, there are Analytics and Blockchain & IoT modules for connecting all supply chain aspects and obtaining advanced insights into every single operation.
Who can benefit from it? While having among its clients multibillion-dollar businesses Aurobindo Pharma and Symantec, Oracle also attracts small-to-medium businesses offering them affordable prices and flexible software solutions. Oracle SCM Cloud promises to boost business growth. However, it’s worth noting that implementation of the system requires significant financial investments and time-consuming workforce upskilling.
Blue Yonder’s Luminate Platform: an intelligent, industry-focused solution for retail
SCM is a key priority of Blue Yonder (formerly JDA Software Group), headquartered in Arizona and owned by the Panasonic conglomerate. The company has been invested in innovation since 1985, and in 2022, Blue Yonder was recognized as a leader in the three Gartner Magic Quadrant reports covering Warehouse Management Systems, Transportation Management Systems, and Supply Chain Planning Solutions.
Luminate™, Blue Yonder’s digital fulfillment platform, harnesses advanced analytics, IoT, AI, and ML capabilities along with digital twin technology and cross-platform integrations to predict disruptions, make forecasts, and draw useful insights from real-time data. The portfolio of highly intelligent software products is divided into three solution categories.
Supply Chain Planning is a powerful predictive technology that handles
- demand forecasting,
- production planning,
- disruptions management, and more.
Supply Chain Execution, also called Luminate® Logistics, is a comprehensive logistics management platform encompassing
- warehouse management,
- transportation management,
- labor management,
- load planning,
- robotics hub functionality, etc.
Omni-Channel Commerce is designed for non-production businesses and focuses on
- inventory management,
- order fulfillment,
- pricing and promotions,
- assortment management, and so on.
Who can benefit from it? The core focus of Blue Yonder is the retail sector. Besides common supply chain modules, the platform contains additional tailored solutions such as retail planning and merchandise management. Yet, it also has offerings for manufacturers, distributors, and logistics companies. Complexity and high prices make this system a bad fit for small companies.
Logility Digital Supply Chain Platform: a modular, highly customizable solution for big and mid-size companies
Logility, a supply chain management software developer from Atlanta, offers customizable modules that easily integrate with each other and work together for a common goal.
- The Demand module takes care of demand planning and optimization, as well as price and promotional analysis and lifecycle management.
- Supply is designed to support procurement, vendor management, production planning, and quality control.
- Inventory helps maintain the right level of stock across all tiers of your supply chain.
- Deploy offers the allocation and automated order promising features.
- Product is about merchandise and assortment planning, a helpful module for retailers that focuses on reviewing, balancing, and updating plans at all levels.
- Integrated business planning helps align financial, sales, production, procurement, and marketing information into a single plan.
- Supply chain data management facilitates integration with multiple IoT devices and other data sources using prebuilt templates, standardized connectors, and rules-based data transformation.
Who can benefit from it? Logility Digital Supply Chain Platform can be customized for different business sizes, from Fortune 500 enterprises to mid-size companies. However, it will be somewhat cumbersome and pricey for small firms. The suite covers the needs of manufacturers, wholesalers, and retailers and is particularly suited for inventory management and demand planning needs.
Niche SCM solutions to manage specific workflows
As you can see, all-inclusive SCM suites are rarely consonant with the requirements of both small businesses and large companies looking to improve one sector rather than reorganizing the entire supply chain. If your scope of SCM work is not that wide, look for the right technology among solutions intended to solve narrower tasks.
Procurement. For example, procurement processes in a small or mid-to-small company can be enhanced by implementing e-sourcing software or a procurement management system that covers the whole buying cycle. Here are a few available options.
- Tradogram is a multi-featured, customizable procurement tool with a free supplier portal that facilitates collaboration and vendor management. It streamlines all purchase-to-pay operations, including spend analytics.
- Procurify handles the entire request-to-purchase-to-pay workflow and offers an easy-to-use mobile app to manage sourcing on the go. It also boasts a convenient in-platform communication tool and multiple integration options out of the box.
- Precoro is a cloud-based procure-to-pay system automating bid comparing, purchase orders, and invoicing. It also tracks spending across the company, having an eye on everything from Internet expenses to office purchases.
- ProcurePort combines spend analysis, e-sourcing, P2P operations, and contract management. The competitive advantages of the e-procurement platform are ease of integration with 3rd party ERPs and a responsive support team.
Inventory. If your key priority is enhancing inventory management, consider the following systems.
- Megaventory covers multi-location inventory management, order fulfillment, report creation, and manufacturing tracking.
- QuickBooks Commerce (formerly TradeGecko) is a cloud-based platform with a convenient inventory controlling component, the ability to synchronize orders from multiple channels, and accurate, real-time report generation features.
- Unleashed Software offers real-time inventory control and reporting. The solution is especially recommended for small eCommerce businesses.
eCommerce fulfillment. An inventory plus shipping combo can be most helpful for small-to-medium eCommerce companies striving to grow. A good example is Ordoro, a one-stop app for inventory control, barcode scanning, shipping order, and drop-shipping.
If you only need help with your shipments, there is ShipBob – an omnichannel fulfillment platform with numerous prebuilt integrations with carriers, marketplaces, and so on. Other affordable multicarrier shipping tools that facilitate eCommerce fulfillment are Shippo, Easyship, and Shippit.
Logistics. When it comes to transportation, small-to-medium companies may consider Magaya, a freight management solution that covers warehousing and cargo operations. Among other useful features, the vendor offers its LiveTrack plug-in for real-time cargo control.
Another warehousing and transportation set tailored for small and medium businesses is Da Vinci, a cloud-based solution equipped with barcode scanning, a yard management component, and other useful features.
How to choose and implement SCM software for your business
There certainly is no single SCM technology that fits everybody. A complex and pricey package can be a money pit for a small business as it pays for plenty of unnecessary features. By contrast, an enterprise adopting a software solution with limited capabilities will hardly reach ambitious business goals. Here are some practical tips to help you choose the right option and avoid costly mistakes.
Estimate the true total cost of ownership. Dive deeper into financial details and add up costs of support, customization, and upgrades. The final number can be impressively larger than the initial purchase price you are ready to pay.
Start with separate, focused modules. Rather than investing in a large, stand-alone SCM system, you can start by implementing a few modules addressing major problems and bottlenecks across your supply chain.
Be mindful of integrations. If you choose to implement several standalone solutions, it’s crucial to connect them into one system to establish smooth data flow. If you don't, you risk losing information, not to mention the lack of analytics in this case.
Consider custom development. Review your existing software and learn how you can complement it with new SMC components and add-ons. Chances are developing a custom solution tailored to your unique case will be cheaper (at least in terms of time and effort) and bring more value than ready-to-use but hard-to-integrate software with functionality that exceeds your needs.
Opt for industry-specific tools. Domain focus is something you shouldn’t ignore. If SCM software is initially designed for a different industry, modification can be a tricky and expensive task.
If there is no proper solution for your niche, explore portfolios of software development teams with relevant expertise. If they successfully launched business process management projects for a company similar to yours, you can count on them to efficiently solve your task as well.
To read more about supply chains, you can visit the transportation section in our blog or check our other articles:
Logistics management systems
Fleet management software
Connecting to transport providers
Integrating shipment carriers
Transportation management systems
Telematics systems
Shipment tracking integration
Supply chain analytics
Fleet and vehicle routing
Load planning
Cold chain logistics
Reverse logistics
eCommerce shipping
Freight broker software
Digital transformation in retail