The COVID-19 pandemic acutely highlighted the fragility of global supply chains. Congested ports, workforce shortages, and production shutdowns were among the many reasons why suppliers struggled to satisfy surging demand. The Russian invasion of Ukraine in 2022 aggravated the problem even more.
The unprecedented strain on the global supply system caused governments and international organizations to take measures in an attempt to solve the issue. For example, the latest initiative is the creation of the Council on Supply Chain Resilience (CSCR) in late November 2023, which aims to support the US supply networks.
But apart from governmental efforts, every business must strengthen its own supply chains to withstand the never-ending turmoil. In this post, we explore the strategies and technologies that can help your company remain stable amid global turbulence.
What is supply chain resilience?
Supply chain resilience refers to an organization's ability to effectively adapt to change and recover from disruptions or unexpected events within its supply chain network. These disruptions include natural disasters, economic crises, geopolitical conflicts, or any other unforeseen circumstances that can interrupt the flow of goods, services, or information.
The key characteristic of a resilient supply chain is agility because timely reaction to disruptions minimizes negative impact on operations. However, the greatest resilience is achieved when a company is able to anticipate future risks and proactively address them.
To get a broader picture of global supply chains and related issues, we suggest a brief overview of the current state of affairs. If you already have an understanding of what’s happening in the industry, feel free to get straight to the next section, where we talk about how to build the sought-after resilience.
Why supply chain resilience is so important
Since supply chains are usually far from being linear, they aren’t really chains. Instead, they are complex, intertwined networks of suppliers, carriers, and other partners involved in the production, storage, and delivery of parts and goods.
For example, Tesla relies on more than 300 suppliers for 2,000 parts to produce its Model S. Apple has disclosed its list of 200 suppliers that make up 98 percent of its materials spend. Retail networks are even larger: For example, Walmart works with tens of thousands of providers globally. Not to mention carriers and intermediaries involved in the sourcing process.
However, when a big retailer like Walmart doesn’t get, say, a load of corn flakes because of the carrier delay, it’s not that big of a deal as there is lots of other merchandise to fill the shelves with. But if an automaker has a container of tires stuck in a port, it won’t be able to produce cars at all.
One can say cars or smartphones aren’t essential goods, but how about the pharmaceutical industry that relies on ingredients made in China? And those are just a few examples. During the pandemic, all industries felt a negative impact because of the domino effect of multiple disruptions worldwide.
The COVID-19 crisis started with factory closures in China. Economic troubles followed closely as lockdowns stopped business activities and affected global supply chains. A sharp economic rebound in Q3 of 2020 created another crisis as companies didn't anticipate a rise in demand accurately. With long delivery times, shortages of materials, and surging container prices, producers couldn’t respond to consumer needs.
That’s when supply chain resilience emerged as a critical strategic focus for companies. Businesses realized that to successfully navigate uncertain times, they must rebuild their supply chains to make them flexible, adaptable, and insensitive to diverse disruptions. But before developing the risk mitigation strategy, you have to first understand which threats you might be facing.
Main supply chain challenges and risks
Various factors can disrupt operations, increase costs, and affect the overall efficiency and effectiveness of the supply chain. Here are the main ones.
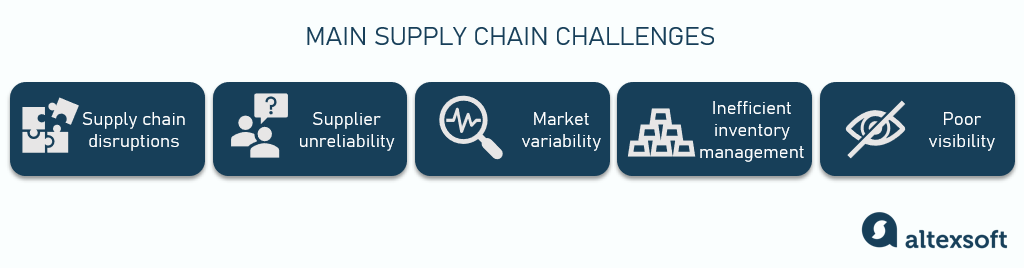
Supply chain challenges
Supply chain disruptions. Besides major disruptions like natural disasters or geopolitical conflicts, there’s always a risk of minor, mundane troubles like flat tires, bad weather, or freight damage. No matter the size of an issue, all disruptions lead to delivery delays, inventory shortages, and increased costs.
Supplier unreliability. Overreliance on a single or a limited number of providers can make the supply chain vulnerable to disruptions caused by supplier bankruptcies, quality issues, or capacity constraints.
Market variability. Fluctuations in customer demand, seasonal changes, and unexpected spikes in orders can challenge inventory management, production planning, and logistics.
Inefficient inventory management. Striking the right balance between having adequate inventory to meet demand and not keeping too much stock (to minimize holding costs and avoid obsolescence risk) is a constant challenge.
Poor visibility. Blind spots in the supply chain and lack of a complete operational picture are the causes of late, often ineffective reactions in case issues arise.
Other challenges often faced by supply chain managers are
- regulatory compliance issues,
- labor-related problems,
- transportation inefficiencies and constraints,
- environmental concerns and requirements,
- cybersecurity threats, and so on.
To manage your supply chain effectively, you must identify and mitigate these risks and challenges, as well as look for opportunities to improve and innovate. So let’s now talk about the strategies that can help you increase your supply chain resilience.
Supply chain resilience strategies and technologies to support them
If old best practices don’t work, you must implement new ones. Here, we suggest several actionable strategies to adjust your operations – and technologies that can make them work better.
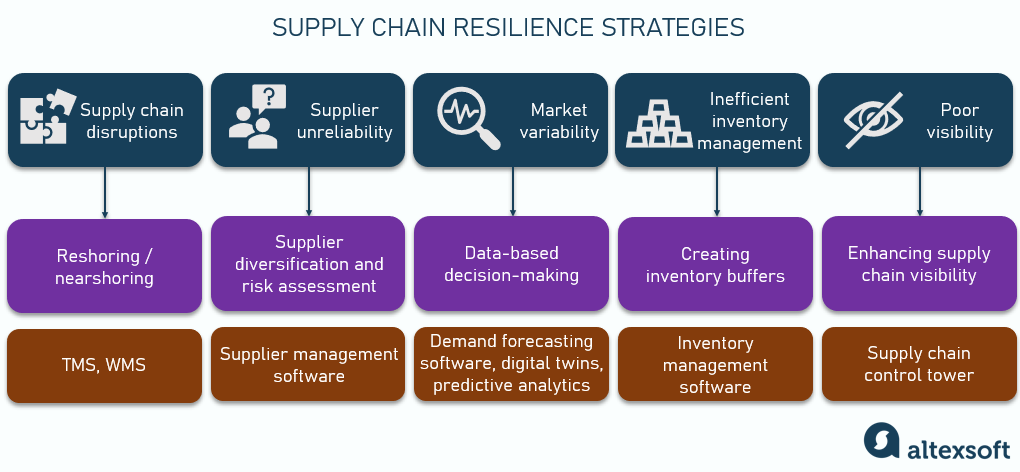
Strategies and technologies for building a resilient supply chain
Most strategies are about taking precautionary measures to minimize potential risks, getting a better understanding of your operations, and developing contingency plans. Note though that all businesses are different and have different operational models and related difficulties, so we can’t give you a universal scenario to act on. You’ll have to choose the strategies that will be most beneficial for your company and tailor them to your specific needs.
Reshoring or nearshoring: Think local
Challenge addressed: supply chain disruptions
Reshoring (or backshoring), as opposed to offshoring, means bringing production or other operational processes back to the company’s home country. It can also be about switching to local suppliers instead of buying materials/goods overseas (then it’s often called regional or local sourcing).
Nearshoring means relocating production or sourcing materials from providers in neighboring countries.
These strategies will help you shorten your supply chain, which, in turn, can safeguard you from disruptions in international freight movement such as clogged ports or Houthi attacks in the Red Sea.
When you do international business, you typically work with freight forwarders who help you arrange cross-border shipping. If you operate within one country, you can also outsource logistics to third-party providers (3PLs) – or organize everything yourself: from production to storage to distribution to last mile delivery. It’s quite an endeavor for sure, but this way you’ll have maximum control over your operations.
Technology to support the strategy: supply chain management software, transportation management system, warehouse management system
Reshoring/nearshoring is mostly an operational strategy when you have to change the way you work. Technology can only support it and optimize your activities, but the choice of tools will depend on the structure of your supply chain. You might already have a supply chain management (SCM) system in use, but you might want to enhance some of its features or add more focused modules.
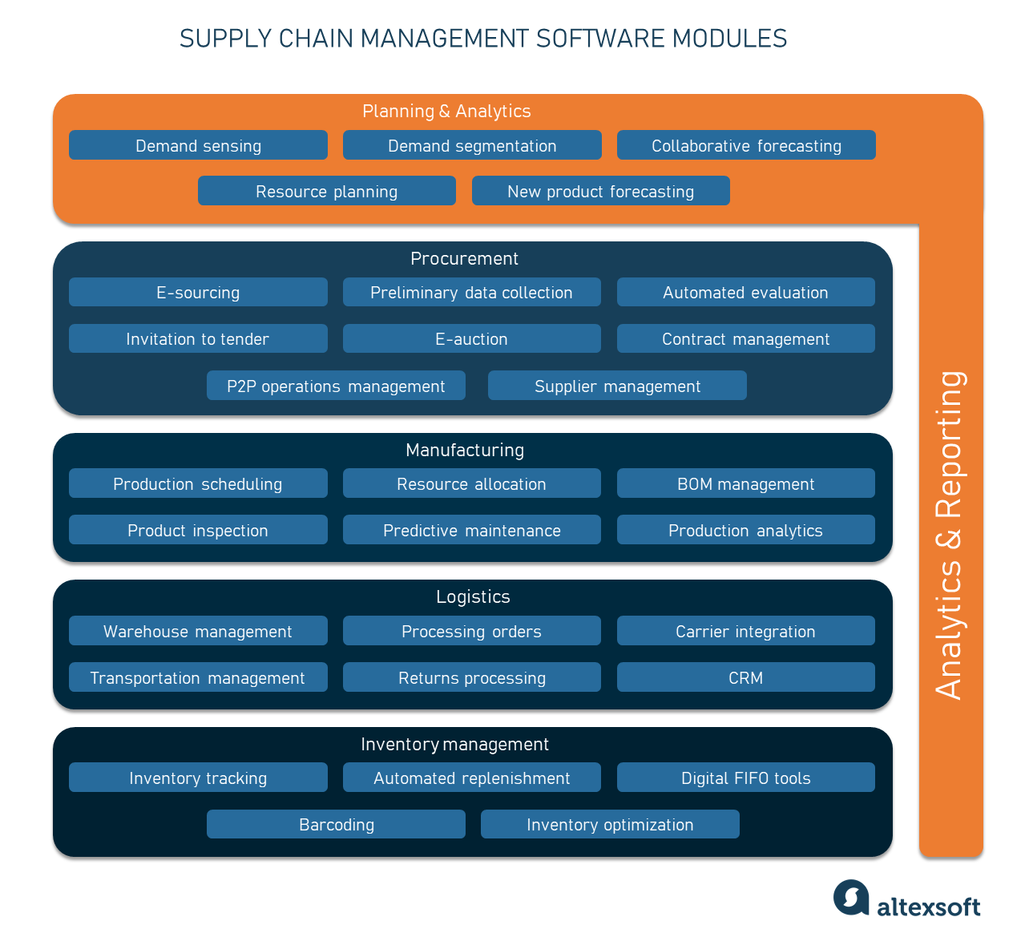
Supply chain management software capabilities
For example, you most likely will need a transportation management system (TMS) to oversee the movement of goods. Among its other features, a TMS will allow you to track the status of your shipments and have a convenient communication channel with carriers and providers. In case something goes wrong, you’ll get an immediate alert, so that you can promptly address the issue.
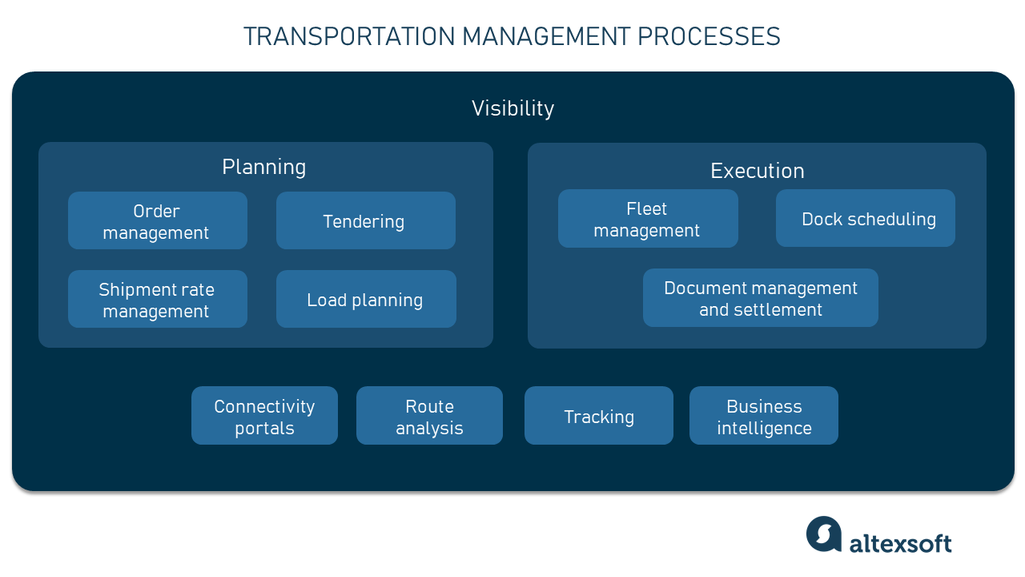
TMS functionality
Also, a TMS can serve as a database of partners (suppliers, carriers, etc.), so in case someone lets you down, you can quickly find an alternative.
If you decide to operate a storage facility and/or distribution center as you reshore your supply chain, warehouse management software (WMS) will help you streamline your workflows. A good WMS will support you on your way to resilience with its asset tracking and inventory management features.
Just like other types of software, it also contributes to providing you with a complete, real-time picture of what’s happening in your business. You must be totally informed to timely identify problems and respond to them. Moreover, an AI-enhanced WMS with an advanced analytical module will help you forecast potential troubles so that you can guard yourself against them.
Supplier diversification and risk assessment: Put your eggs in different baskets
Challenge addressed: supplier unreliability
The goal of any diversification is to reduce risk. In this case, diversification means sourcing from multiple suppliers or manufacturing in different regions or countries. That will reduce your reliance on a single source for critical components or materials.
Identify alternative suppliers and build relationships with them in advance to create redundancy and safeguard your procurement. And regularly evaluate your partners’ reliability.
Technology to support the strategy: supplier (vendor) management software
Modern AI-based supplier management solutions can help you audit your supplier network, assess their performance, and identify risks before issues arise. Regular tracking of partners’ performance helps in identifying consistent issues or declines in efficiency, which can indicate potential risks.
Such software rates your partners so that you can see the level of risk each supplier presents. It assigns scores based on various parameters like past performance, delivery timelines, quality of goods, and reliability. Once the platform identifies and assesses risks, it can help you develop mitigation strategies, e.g., creating contingency plans or setting up stricter quality controls.
This software also ensures that your partners comply with industry standards and regulations. That reduces the risk of legal penalties or reputational damage due to noncompliance. The system will send you alerts in case of any deviations from agreed terms (such as delayed shipments or quality issues) so that you keep abreast of the supplier’s activities and timely react if needed.
Also, there’s often a supplier-facing portal to facilitate your interactions. Transparent communication leads to easier problem-solving while maintaining healthy business relationships.
Besides, these platforms automate many time-consuming workflows such as qualification and onboarding, contract management, communication and document exchange, product inspection, and so on.
Supplier management systems often come as modules of comprehensive ERP, e-procurement, or SCM solutions. In this case, they seamlessly integrate with other business management modules which enables an efficient data exchange. Some examples of such platforms are SAP Ariba, GEP SMART, Coupa, and Oracle SCM.
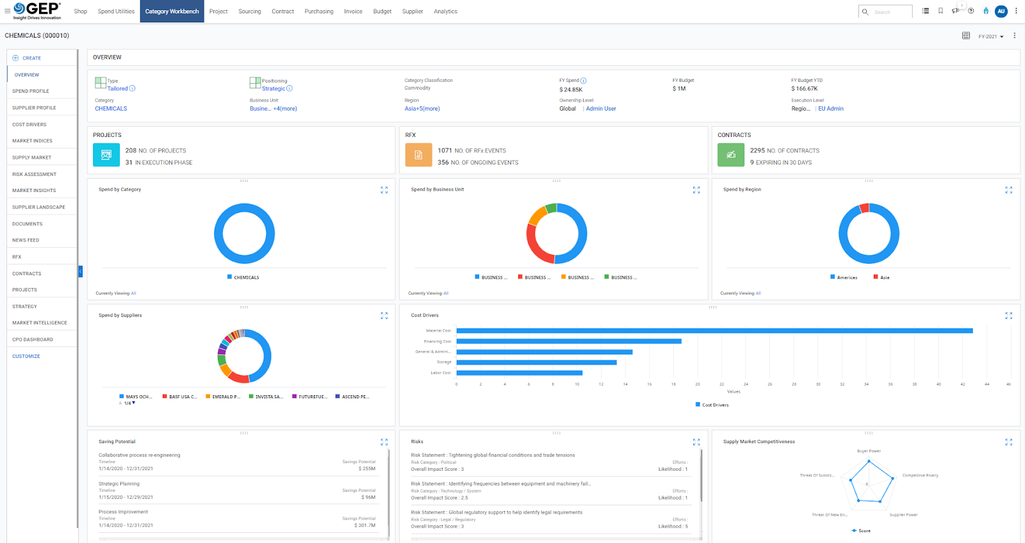
Dashboard interface of GEP SMART
If you need a more focused solution to cover this specific business aspect, you can check out specialized systems such as Precoro, AdaptOne, or Sirion.
Data-based decision-making: Anticipate market behavior
Challenge addressed: market variability
It’s obvious that you can’t predict all supply chain disruptions (e.g., natural cataclysms, terrorist activity, or a huge containership stuck in the Suez Canal for six days). But you can still make some forecasts to base your decisions on.
Let’s take, for example, demand as the most crucial aspect you base your planning on. There are two main types of demand forecasting. One is a traditional approach based on statistical methods. It works well in stable market conditions, but unfortunately, it’s of little use in times of uncertainty. The other approach uses ML techniques to make accurate predictions in volatile markets.
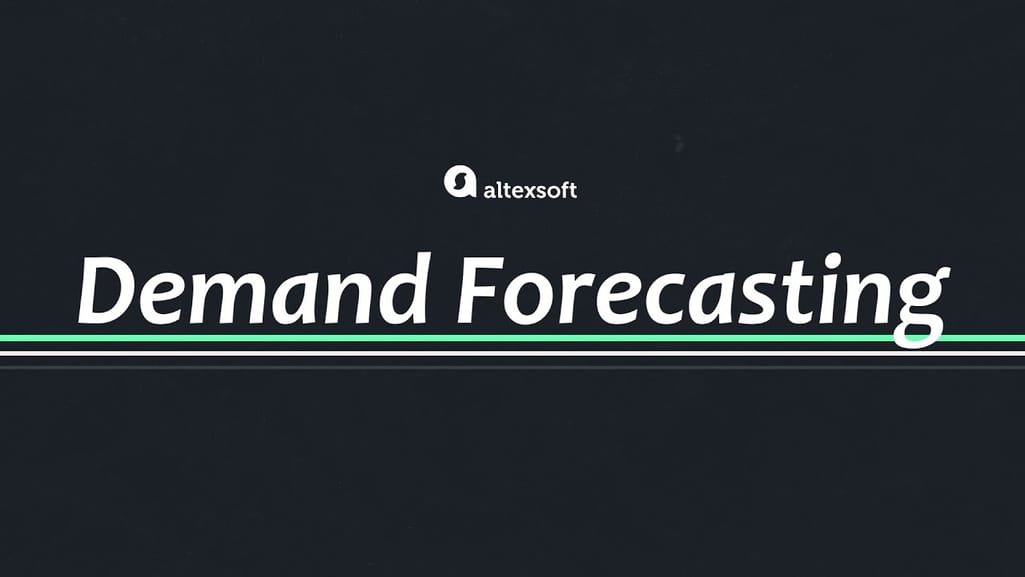
How demand forecasting works
Implementing advanced analytical software will allow you to base your decisions and strategies on accurate data rather than guesswork. You’ll be able to anticipate market fluctuations and adjust your procurement, capacity planning, and marketing activities.
Technology to support the strategy: demand forecasting software, digital twins, predictive analytics
Demand forecasting software generates short- and long-term predictions for different groups of products or separate items. It supports planning for multiple regions and sales channels. You’ll be able to simulate and compare different what-if scenarios, e.g., when you launch new products, plan a promotion, change prices or assortment, etc.
As for specific products, almost any supply chain management or inventory management platform today has demand forecasting functionality. There are also more focused planning tools like o9, Retalon, or Fountain9 you can check out. Or you might want to build a custom demand forecasting module to fit your unique business requirements.
Digital twins is a technology that creates a virtual replica of the supply chain, enabling real-time monitoring and tracking of assets, products, and processes. Digital twins analyze data and simulate different operational strategies. Such simulations allow you to predict potential issues before they occur, e.g., market changes, supply interruptions, or logistical challenges. If you identify vulnerabilities in advance, you can take proactive measures and create contingency plans.
Predictive analytics is using machine learning techniques to make accurate forecasts based on big data. It requires building a data infrastructure to collect, store, and process information from different sources. Please check the related articles below to learn more about it.
Creating inventory buffers: From just in time to just in case
Challenge addressed: inefficient inventory management
Many companies used to implement a just in time approach to inventory management, which allowed them to minimize holding costs. However, it made their supply chains more vulnerable to disruptions.
During the pandemic, a lot of businesses switched to a just in case approach and increased their inventory levels of critical components and materials. Holding larger safety stocks allowed them to buffer against supply chain glitches.
However, it's still essential to strike a balance between excess stock and carrying costs. Data-driven optimization of inventory is the key to this problem.
Technology to support the strategy: inventory management software
Advanced demand forecasting and predictive analytics are definitely the core of modern inventory management software (IMS). Based on accurate forecasts, you’ll be able to adjust your inventory levels proactively, reducing the risk of shortages or surpluses.
Its other major benefit is inventory tracking and visibility into stock-related activities. The IMS will allow you to track the movement of all SKUs (stock keeping units) and have a granular picture of inventory levels across various locations. Transparency and traceability throughout the supply are crucial for quickly addressing issues and for compliance with regulatory requirements.
A good IMS will not only help you balance supply and demand but also prioritize items to source. Its other features usually include
- automated reordering,
- space optimization,
- sales management,
- order processing,
- reporting, etc.
Again, there’s no single recommendation. You’ll have to research different solutions, compare their functionality and compatibility, and find what’s right for your needs.
Enhancing supply chain visibility: See the full picture
Challenge addressed: poor visibility
It’s barely possible to adapt to market conditions without having a complete understanding of internal and external situations. If you don’t know what is happening in your organization or along your supply chain, you can’t control it or timely respond to disruptions. Decision-making becomes based more on guesswork than on solid information.
Technology to support the strategy: supply chain control tower
Supply chain control towers (SCCT) provide real-time, end-to-end visibility into your operational workflows. You’ll be able to track and trace all the goods throughout every stage and across all the tiers of the supply chain. You’ll have complete information about your partners and your interactions with them, while being able to control your spending and monitor your performance.
Having such a holistic picture will support your decision-making which, in turn, will increase business efficiency and, ultimately, affect the bottom line. You’ll be able to identify potential disruptions early and respond proactively.
The complex part here is that the SCCT isn’t a ready-made solution you can just buy, install, and start using the next day. It’s a multi-component structure that includes all your internal IT tools, as well as third-party systems (e.g., that of your partners) and external data sources.
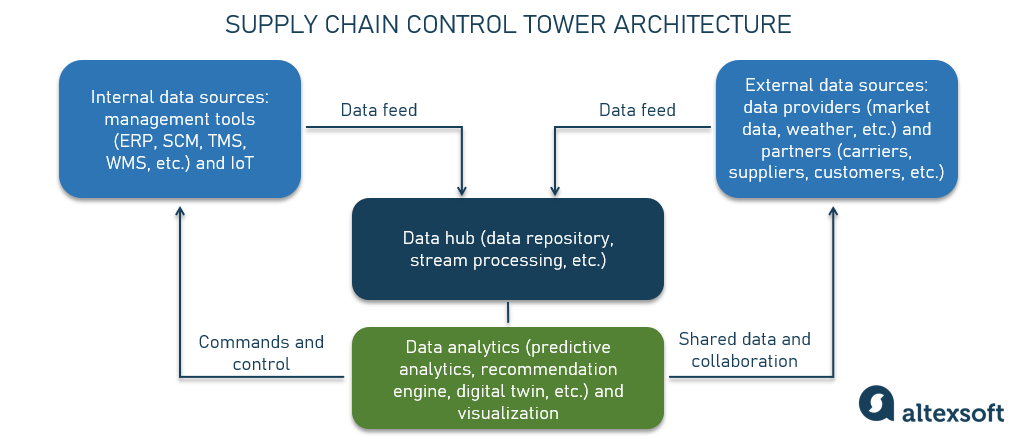
Control tower architecture
It also usually involves developing an IoT infrastructure to gather real-time data from storage, equipment, and shipments.
If you decide to build your own SCCT, you’ll have to develop the data infrastructure we mentioned above. There are vendors that offer an SCCT platform (e.g., One Network, Kinaxis, or Blue Yonder), but keep in mind you’ll still need to tailor them to your needs.
Building and maintaining a resilient supply chain is an ongoing process that requires commitment, investment, and adaptability. By proactively addressing risks and implementing these strategies, organizations can better prepare themselves to navigate disruptions and uncertainties while maintaining a robust and efficient supply chain.
And yes, changes always require investment – but compare the cost of implementing new software and practices with the cost of losing your business because of supply chain disruptions.
Speaking about costs and numbers, let’s talk about how you can understand how resilient your supply chain is.
How to measure supply chain resilience?
Measuring supply chain resilience involves a range of metrics that help evaluate how well a supply chain can anticipate, respond to, recover, and adapt to unexpected disruptions. Here’s what you can track.
Time to recover. The main resilience metric is time to recover (TTR) – the time your company needs to restore normal functioning after disruptions. A short recovery period indicates a resilient and agile supply chain.
Forecast error. We’ve talked a lot about the importance of accurate predictions. Forecast error helps understand how precisely you can anticipate future events. The point is to compare the forecasted values (what you expected to happen) against the actual values (what actually happened) and calculate the difference. The smaller this discrepancy is, the better.
You can use various statistical methods, such as Mean Absolute Error (MAE), Mean Squared Error (MSE), or Mean Absolute Percentage Error (MAPE).
Inventory management efficiency. Stock-related metrics such as inventory turnover ratio or days of inventory on hand can indicate how well a supply chain manages stock to handle fluctuations in demand or supply.
Customer satisfaction and retention. Metrics related to customer service -- such as order fulfillment rates, on-time delivery rates, and customer complaints -- can indicate how disruptions are affecting end customers. If customer satisfaction is stable despite any issues in your company, it’s a good sign.
Supplier diversification. To assess the extent to which a supply chain relies on a broad base of suppliers rather than a few, monitor the percentage of total spending or critical components sourced from a single supplier.
Supply chain performance metrics. Monitoring the fluctuations of supply chain KPIs like order lead time, supply chain cycle time, and throughput efficiency also helps understand how well you perform – and how stable your business is.
These measurements, used collectively, provide a comprehensive picture of the resilience of a supply chain. They help to identify vulnerabilities, evaluate the effectiveness of current strategies, and guide improvements for better handling of future disruptions.
Now, for inspiration, we suggest you look at some examples of how other companies adapted their operations to overcome supply chain issues.
Agile supply chain examples
As we said, after a cold shower-type “wake-up call” in 2020, many global companies have recognized the importance of building agile supply chains and have successfully implemented strategies to enhance their stability. While specific approaches may vary, here are a few examples of companies that have demonstrated resilience in their supply networks.
Apple
One of the biggest global companies, Apple was heavily reliant on its Chinese partners for materials and production. In recent years, the company launched manufacturing facilities in India, Vietnam, and other countries. Also, it diversified its supplier base, reducing its reliance on any single supplier for critical components like iPhone and iPad screens, and started building a logistics hub in Saudi Arabia. In addition, Apple is working with its most critical component providers (like TSMC) on the strategy of moving production to Europe and the US.
To manage its supply chain most effectively, Apple has developed advanced ML-based software to make accurate predictions, get insights into its operations, and support decision-making. Besides, the company invests heavily in supply chain visibility and traceability, using blockchain technology to track and verify the origins of materials used in its products.
Apple has also been investing in educating employees along its supply chain since 2008. In 2022, it partnered with the International Labour Organization, the International Organization for Migration, and global education experts to launch a $50 million Supplier Employee Development Fund. Through these educational initiatives, Apple increases the quality of its supply chain and promotes manufacturing best practices.
Amazon
Amazon has a highly flexible and agile supply chain network that can quickly adapt to changes in customer demand and market conditions. It has invested in innovative technology, including advanced robotics and automation, to optimize its fulfillment centers and improve efficiency.
During the COVID-19 pandemic, Amazon reacted quickly by implementing safety measures and operational adjustments to continue delivering essential goods to customers, which demonstrated its adaptability.
Toyota
Toyota is known for its just-in-time (JIT) production system, which relies on close collaboration with suppliers to ensure a steady flow of parts and components. However, when the shortage of semiconductors and chips impacted the company's performance, it reconsidered its approach and increased the supply of critical components. Plus, to safeguard itself from provider-related risks, Toyota has created a diversified global supplier network.
Also, Toyota has an agile culture of continuous improvement (Kaizen), which is about immediately making necessary adjustments in response to changing conditions.
Procter & Gamble (P&G)
P&G has a robust risk management strategy that involves scenario planning and simulations to prepare for various disruptions. It maintains a high level of inventory for certain critical products to ensure supply continuity during emergencies.
P&G partnered with data science expert KNIME to develop a robust demand forecasting solution. The company’s focus on visibility and data analytics helps it monitor supply chain performance and make proactive decisions.
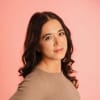
Maria is a curious researcher, passionate about discovering how technologies change the world. She started her career in logistics but has dedicated the last five years to exploring travel tech, large travel businesses, and product management best practices.
Want to write an article for our blog? Read our requirements and guidelines to become a contributor.