Prevention is better than cure.
If you think vehicle breakdowns are inevitable, we've got news for you. Veteran truck drivers believe, “If handled and driven correctly and the maintenance and inspections are performed religiously, you may never suffer a breakdown.”
Fleet owners in trucking, car rental, delivery, and other transportation companies know that poorly maintained vehicles burn more fuel and can conk out every other mile. And breakdowns are just too expensive, especially at a fleet-wide scale (not to mention risking drivers’ lives, losses due to unfulfilled contracts and related downtime, and customer dissatisfaction).
These risks and losses can – and must! – be avoided with proactive maintenance. We’re not gonna talk about those oil changes and tire rotations – you already know about those. We’ll talk about the general approach and how software can help you as a fleet manager or owner cope with your maintenance activities and avoid those costly unplanned repairs.
Types of maintenance: reactive vs preventive vs predictive
As we discussed in one of our previous articles, there are three main types of maintenance policies: reactive, preventive, and predictive (the two latter categories are referred to as proactive maintenance). Here, we’ll briefly recap the main pros and cons of each.
Reactive vs preventive vs predictive
Reactive or corrective maintenance is fixing equipment only when it breaks. It requires less planning and seemingly allows for savings on support maintenance, but usually leads to extra expenses due to higher repair costs. It takes about four times more money to repair roadside truck breakdowns than it does handling issues in your own shop. Besides, such an approach is associated with safety risks, unaffordable lengthy downtime, and decreased equipment useful life.
Preventive maintenance is about conducting systematic inspections and following a plan of regular maintenance activities, which is usually based on time or mileage intervals.
Taking good care of your fleet assets pays off by prolonging their lifecycle, increasing efficiency, and reducing the probability of failures. Frequent checks also allow you to discover possible problems before they grow big. However, serious failures can still occur with preventive strategy. Another downside is that more planning is required and downtime is significant because of regular maintenance.
Predictive maintenance (PdM) involves constant monitoring of your equipment condition and conducting repairs only when bad trends are detected – but before breakdowns occur. Such an approach requires a great deal of investment since a whole ecosystem has to be created, including IoT sensor installation, acquiring specialized software, creating and maintaining machine learning (ML) models, engaging IT and data science specialists, and so on. Data is gathered from connected sensors and analyzed so that predictions of possible failures can be generated.
All these efforts bring about a truckload of perks such as reduced maintenance time and cost, prolonged equipment lifespan, increased uptime, and so on.
Out of the three strategies, reactive maintenance has proved to be inefficient and costly in the long run, so most fleet owners adopt a proactive approach. Let’s explore how software can streamline your fleet maintenance activities and what technicalities are behind those proactive strategies.
Preventive maintenance software: supporting planned service activities
Preventive maintenance is a traditional, universally adopted approach. As we said, it’s basically about regular checks and prescheduled service. Federal Motor Carrier Safety Administration Regulations establish standards of daily and annual inspections, while manufacturers always provide the recommended maintenance schedule to prolong equipment lifespan. If you operate a big fleet, all that can translate into quite a workload.
Managing your fleet maintenance activities with spreadsheets and sticky notes that remind you about the next oil change due date isn’t the best idea. So, what’s the alternative?
Technological solutions to fleet maintenance
To support your preventive maintenance strategy, you have two technical options.
- You can adopt a comprehensive fleet management system that has vehicle maintenance as one of its modules. Such providers as Teletrac or Fleetio offer robust, multifunctional platforms that enable vehicle tracking, routing, dispatch, fuel management, and more. Check our article on fleet management software for details.
- If, for example, your fleet management system doesn’t have that maintenance module, you can implement specialized fleet maintenance software. In a broader sense, it can also be called a computerized maintenance management system or CMMS (the difference is that a CMMS can be used in other industries as well). Options are many; you can check AUTOsist, FleetSoft, or Fleet Maintenance Pro to build a picture.
Whichever option you choose, there are a number of core features that you should be looking for if you want to actually make your life easier.
Fleet maintenance software features
A fleet maintenance system serves as a database of all your assets since it stores important vehicle- and service-related information. It also helps automate related operations and gives you visibility into what’s going on.
Fleet maintenance software features
Maintenance alerts can be set up for each vehicle to notify managers and drivers of the scheduled check-ups and/or service.
Service history allows you to keep detailed records of all the repairs, track costs, and analyze equipment cost-effectiveness.
Electronic DVIR filing is a huge time-saver for drivers, letting them complete and submit their inspection reports right from their smartphone or tablet. For fleet managers/owners, having all documentation in one system is what provides an understanding of the entire fleet condition.
Inventory management allows you to track parts and avoid shortages.
Inventory module on Fleetio
Work order management is convenient for drivers who can easily take a photo of the breakage and create a work order, for managers who can assign repairs and plan on parts replenishment, and for mechanics teams that have a clear picture of their schedule. Work orders can also be triggered automatically based on mileage, run hours, etc. On completion, the amount of parts in stock is updated and repair information is saved to service history.
Work orders dashboard in Fleet Maintenance Pro
Reporting and analytics is essential to obtain a bird's eye view of your fleet and make data-based decisions. You’ll be able to analyze asset availability, repair costs, parts usage trends, labor costs, etc.
Some systems offer additional functions such as fuel tracking, trip logs, documentation management (for example, insurance and registration cards), etc. Also, having a connected driver app is essential to support communication and have access to unified data in a single system.
Speaking of unification… To provide the best results, software has to be connected with your other internal systems. Let’s talk about how integrations can be helpful.
Fleet maintenance software integrations
If data is siloed, you can’t use it effectively and benefit from it. Integration, or connecting separate systems via APIs to establish a two-way information exchange, is key to efficient process automation and obtaining an accurate overview of your fleet condition, operations, and performance. You can establish internal and external integrations (which ones you require depend on your specific business model and needs).
Fleet maintenance software internal and external integrations
Integration with a fleet management system (or other trucking software) allows you to share equipment databases, plan trips considering service schedules, share expense information, and much more.
Integration with telematics systems opens the door to a wide range of crucial vehicle-related data. You can receive diagnostic reports, odometer readings, fault codes, and so on.
Integration with inventory management software is necessary if you stockpile parts and equipment and want to control inventory. In this case, you’ll always know what you have on hand, where it is, and when it has to be replenished to avoid shortages.
Integration with a business intelligence tool is important for receiving a holistic analysis of your maintenance processes, tracking costs, visualizing trends, and getting actionable insights.
Integration with scheduling software supports your workforce management and helps organize service teams shifts.
Integration with a fuel management system allows for sharing fuel consumption data. Often, the change in fuel usage can signal malfunction. If you don’t have one, but still want to track fuel metrics, there’s an alternative.
Integration with a fuel card or external fueling system will also provide you with reports on fuel consumption.
Integration with parts and/or service providers enables cross-company data exchange and can streamline your relationships with your business partners.
Integration with a vehicle specification database allows you to receive accurate technical information on any vehicle, as well as service, maintenance, and repair cost forecasts. Some examples of such industry data providers are JATO, HaynesPro, or HPI.
Fleetio offers an out-of-the-box integration with DataOne vehicle specs database
You can see how system integrations can streamline processes, so consider building such connections to increase efficiency. Just note that developing customized infrastructure requires investment and assistance from an experienced integration provider.
Bottomline: Preventive maintenance, when approached systematically and supported by the right instruments, can be effective and allow you to save money and increase the equipment useful life. But! It means taking a vehicle out of rotation every few thousand miles (or every few months) for scheduled maintenance. Is this downtime really that necessary?
Predictive maintenance: building custom data infrastructure
Predictive maintenance, contrasted with preventive maintenance, allows you to take the vehicle to the service shop only when it’s required. But compared to reactive maintenance -- before it breaks down. In this way, you avoid both performing too much upkeep and being late with your repairs.
As we mentioned above, PdM is a complex project that requires significant investment to build a custom hardware and software infrastructure that will collect data from connected IoT devices, analyze it, and trigger relevant maintenance events. So, if you feel you’ve outgrown your preventive strategy and have a budget for development, we’re here to tell you how it works.
Collecting data from connected sensors and external sources
We’ve already mentioned the importance of telematics systems for vehicle diagnostics. So, to enable remote monitoring, you have to install a number of smart IoT devices to collect and transmit your vehicle data such as
- temperature,
- voltage,
- vibration,
- tire pressure,
- fuel consumption,
- engine data,
- transmission data,
- battery condition, and so on.
Monitoring driver behavior is also important since it greatly impacts how fast equipment wears out. To get an even fuller picture and accurately predict the wear and tear of a vehicle's electrical and mechanical parts and components, you can add external information like weather and traffic – both current and forecasted.
It’s an awful lot of data, so it has to be processed with special tools.
Processing data
Telematics data is generated continuously in enormous amounts so it falls under the category of big data. It requires building a complex storage, processing, and analysis architecture. Machine learning (ML) models have to be developed and trained to make predictions using historical and live data.
Recent research has shown that deep learning techniques and digital twin technologies give comparatively accurate results and can predict vehicle performance and probability of breakdowns. At the same time, those novel approaches require more data and greater data engineering efforts than more traditional ML methods.
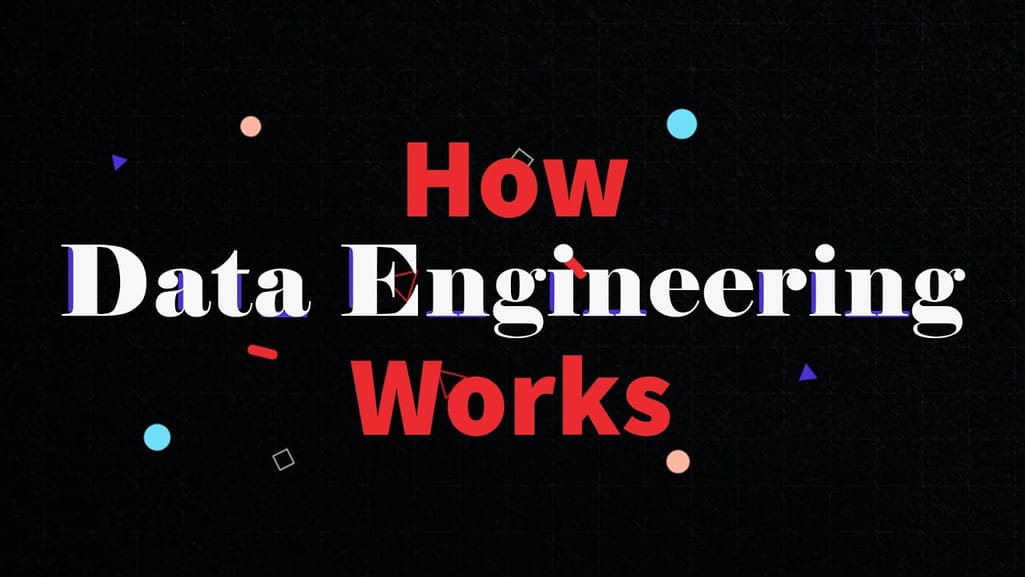
Check our video overview of how data engineering works to get an idea
Traditionally, data was stored and processed on special cloud computing platforms. Recently, the trend is shifting towards edge computing, which means processing data closer to its sources – the sensors.
Analyzing sensor and external data, you not only get a complete understanding of a vehicle’s current condition, but you can also identify abnormal trends, detect faulty behavior, and predict future failures. The fault codes received from various vehicle systems are interpreted and prioritized so you know the severity of issues.
Visualizing and applying analytics results
To get actionable insights from data and make use of analytics results, you have to be able to visualize them in reports and dashboards. You can use any of the mentioned above fleet management or fleet maintenance software since they offer a wide range of convenient, industry-specific reports and metrics.
Trend visualization in the Stratio platform
Knowing the predictions, you can schedule the vehicle for shop diagnostics or service. Or, you can set up a system of business rules that will enable automatic work order generation in case of anticipating severe issues.
What to consider before starting with predictive maintenance
There are a few more things you have to consider before you dive into a full-blown development project.
Time and investment. Once again, be prepared that shifting towards PdM is time- and resource-consuming. Purchasing hardware and software, developing data architecture, and implementing new solutions is a long way to go.
Choosing partners. To build or to buy is the age-old question. Custom solutions perfectly satisfy your business needs, while ready-made systems are typically faster and easier to implement. Speaking of PdM for fleets, a number of providers offer ML-based predictive software, e.g., Noregon, Intellias, or Fiix. The choice is yours, but note, that if you go with an off-the-shelf platform, you’ll still need to do a lot of customizing and fine-tuning.
Training and changing mindset. Remember to conduct proper training for your staff, from drivers to service teams. PdM is very different from what most people are used to, so make sure everyone understands the benefits of a new approach.
Driver app + manager app. The world is going mobile, so having user-friendly apps connected to your business systems is convenient and enables faster communication and data sharing.
Access permissions. Make a set of permission levels to give different departments different access to information and analytics results.
Possibly increased downtime at the beginning. Once you implement a new system, you might identify a lot of failing vehicles in your fleet that require repairs. Be prepared that the first few months your shop will be busy and many vehicles will have to be taken off the road. However, after that initial cleanup, you’ll witness a major uptime increase.
Predictive maintenance use cases
On a final note, let’s look at some real-world industry success cases of implementing predictive maintenance.
United Road plans to save $3,387 per truck yearly
United Road, one of the heavy-haul transportation leaders in North America, partnered with Uptake to conduct proactive maintenance, prevent unexpected roadside breakdowns, and increase driver mileage.
Uptake Radar platform collected data from a telematics provider and historical work order data. Various failure modes were monitored, including plugged diesel particulate filters, NOx sensor failures, exhaust gas recirculation (EGR) valve failures, and coolant leaks.
During the first two months, failures on 29 trucks were predicted, 24 of which were confirmed and repaired in the shop. United Road estimates an average annual saving of $3,387 per vehicle due to its proactive maintenance strategy.
750-vehicle operator saved $71,000 with ML predictions
A long-haul truck company of 750 vehicles implemented the Stratio Predictive Maintenance platform to address air compressor issues. During the second year of utilization, as their ML models were increasing prediction accuracy, 68 road-side breakdowns were forecasted and avoided (from a total of 117 events). This allowed the operator to save €62,600 (around $71,000).
Vehicle manufacturer builds PdM tool to reduce costs and downtime
Navistar is one of the biggest North American manufacturers of heavy-duty vehicles, buses, and diesel engines. They developed an IoT-enabled remote diagnostics platform named OnCommand Connection that consumes 70+ telematics and sensor data feeds from more than 375,000 vehicles. It tracks engine performance, truck speed, acceleration, coolant temperature, and brake wear.
Besides, external data such as meteorological, geolocation, vehicle usage, traffic, historical warranty, and parts inventory information is considered. ML techniques enable advanced analytics to automatically detect engine problems early and predict maintenance requirements. Truck health and performance can be monitored from smartphones or tablets. The platform also prioritizes needed repairs and recommends corrective measures.
As a result, Navistar has been able to reduce maintenance costs and vehicle downtime by almost 40 percent. Moreover, one of their customers reported that the maintenance cost per mile for its vehicles dropped from 12-15 cents to less than 3 cents.